- Calculating Pumping Plant Performance
- Causes for Substandard Performance
- Pump Performance Test Data Analysis
Irrigation pumping plant performance can be easily determined in the field with a few simple calculations. Standard figures have been developed for comparing pumping plant performances. These standard figures can reasonably be expected from well-designed, well-maintained systems. It is possible to obtain a performance that exceeds the standard.
Pumping plant standards are given in units of water horsepower hours (whp • hr) per gallon or kilowatt-hour of energy consumed. They include all allowances for normal pump efficiencies, drive losses and friction losses in the discharge column and discharge head. Table 1 shows these standards for several energy sources.
Table 1. Nebraska Performance Standards for Irrigation Pumping Plants | |
Fuel | Performance Standard* |
Diesel | 12.5 whp • hr/gal |
Gasoline | 8.55 whp • hr/gal |
Electricity | 0.885 whp • hr/kwh |
LP Gas | 6.89 whp • hr/gal |
* Based on 75% pump efficiency and 5% drive loss for non-electric units. |
A pumping plant test requires measuring the physical properties related to the pump. Pumping rate (gpm), pumping lift, pressure at the discharge outlet, and the amount of fuel consumed over a period of time must be measured while the pump is operating at its normal load.
Calculating Pumping Plant Performance
An example set of field data (below) helps illustrate the procedure for calculating pumping plant performance.
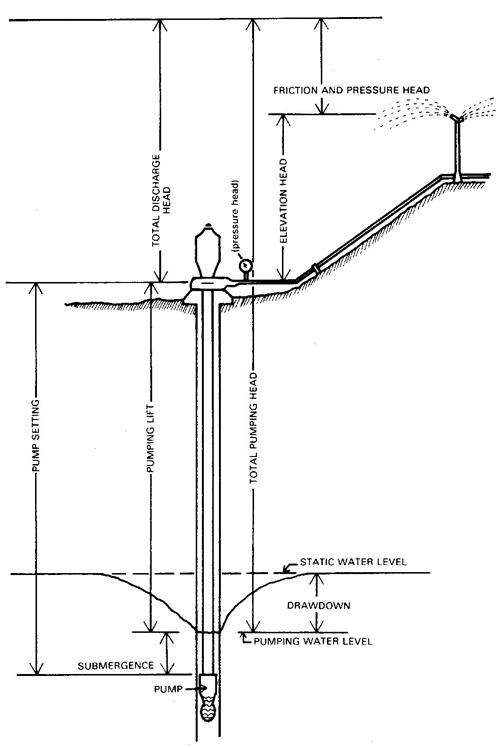
Pump Discharge Rate, Q = 600 gpm
Pumping Lift, Le = 70 ft
Discharge Pressure, P = 60 psi
Pump Speed = 1750 rpm
Pump Test Duration = 1.0 hr
- CheckPump Speed: Measure pump speed with a portable tachometer to ensure that the pump is operating according to its specifications. The pump operating speed should be stamped on a plate attached to the pump discharge head.
In this example, the measured pump speed (1750 rpm) is near the required pump operating speed (1760 rpm). If it was not the case, the speed must be adjusted before continuing. - Calculate Total Pumping Head (TH):
TH = Pumping Lift (ft) + Discharge Pressure (ft)
TH = 70 ft + 60 psi • 2.31 ft/psi (since 1 psi = water column 2.31 ft high)
TH = 70 ft + 139 ft = 209 ft - Calculate Water (Output) Horsepower, WHP:
WHP = Q • TH
3960
WHP = 600 gpm • 209 ft
3960
WHP = 31.7 hp - Calculate Pumping Plant Performance:
Performance (whp • hr/gal) = WHP • Test Duration (hr)
Fuel Consumed (gal)
Performance = 31.7 hp • 1.0 hr
4.0 gal
Performance = 7.9 whp • hr/gal - Calculate Pumping Plant Efficiency, EFF:
EFF = Pumping Plant Performance • 100%
Performance Standard
EFF = 7.9 whp • hr/gal • 100%
12.5 whp • hr/gal
EFF = 63.2% - Calculate Potential Fuel Savings:
Potential Fuel Savings/Hour = Current Fuel Consumption Rate • (1=EFF) • 100%
Potential Fuel Savings/Hour = gal/hr • (1 - 63.2%) • 100%
Potential Fuel Savings/Hour = 1.5 gal/hr
In this example, the actual pumping plant performance of 7.9 whp • hr/gal is 63.2 percent of the performance standard for diesel-powered pumping plants (see Table 1). For the size of unit described, 1.5 gal/hr of diesel fuel is wasted because the pumping plant is not operating efficiently in its current condition. Whether or not this loss in efficiency is significant enough to justify having the pumping unit repaired depends upon the expected repair cost and the number of pump operation hours per year. In general, if the repair cost can be regained by savings in operating costs over two to three years, then it is economically feasible to have the repairs made. The actual repayment time can only be calculated using a detailed economic analysis, which includes the expected efficiency increases, fuel costs and repair costs amortized over that period of time.
Causes for Substandard Performance
Substandard pump performance can be caused by several factors, including the following:
- The pump could be mismatched for present conditions.
The pump may not have been properly selected or the operating conditions may have changed. The water table could have dropped or a new pipeline could have changed the pumping head requirement. The power source may not be operating at the specified speed (rpm) for maximum efficiency. - The impellers could be out of adjustment or damaged.
Qualified repairmen can adjust the impeller clearance with the bowl for the greatest efficiency. If the impeller is badly worn or corroded, adjustment will not help. Cavitation occurs in pumps that attempt to operate at flow rates greater than the well can supply. This pits the impellers and ruins them. - The engine may be loaded improperly.
An internal combustion engine operates most efficiently at 75 to 90 percent of its continuous horsepower rating at its design speed. Electric motors operate best at 100 to 110 percent of their nameplate rating. Overloading an internal combustion engine can seriously shorten engine life and increase fuel costs. - The engine may need a tune-up.
The ignition, timing and carburetion should be adjusted on spark-ignited engines. Diesel engines require fuel injection timing. Adjustments should be made by a qualified specialist to ensure maximum efficiency under the operating conditions. Electric motors generally do not need adjustment, although excessively worn parts should be replaced. Run a compression test to determine if an internal combustion engine needs an overhaul. - The pumping system may be poorly designed.
Poor design elements include an undersized suction pipe, an improperly sized discharge column, restrictions in the intake strainer and misalignment of the drive shaft (indicated by excessive wear). These problems can result in low efficiency ratings.
Pump Performance Test Data Analysis
- Pump Discharge Rate: ___________________gpm
- Pumping Head Pressure: __________________ psi • 2.31 = ___________________ ft
Lift = ___________________ ft
Total Pumping Head = ___________________ ft - Output Water HP: (1) * (2) / 3960 = ___________________ whp
- Fuel Use Rate: ___________________ gal/hr (Internal Combustion)
___________________ kwh/hr (Electric) - Pumping Plant Performance: (3) / (4) = ___________________ whp • hr/ ___________________
- Performance Standard = __________________ whp • hr/ ___________________
- Efficiency = (5) / (6) * 100 = __________________%
Major funding for this program came from the Georgia Office of Energy Resources
Status and Revision History
Published on Jun 25, 2009
Published with Full Review on Jun 22, 2012