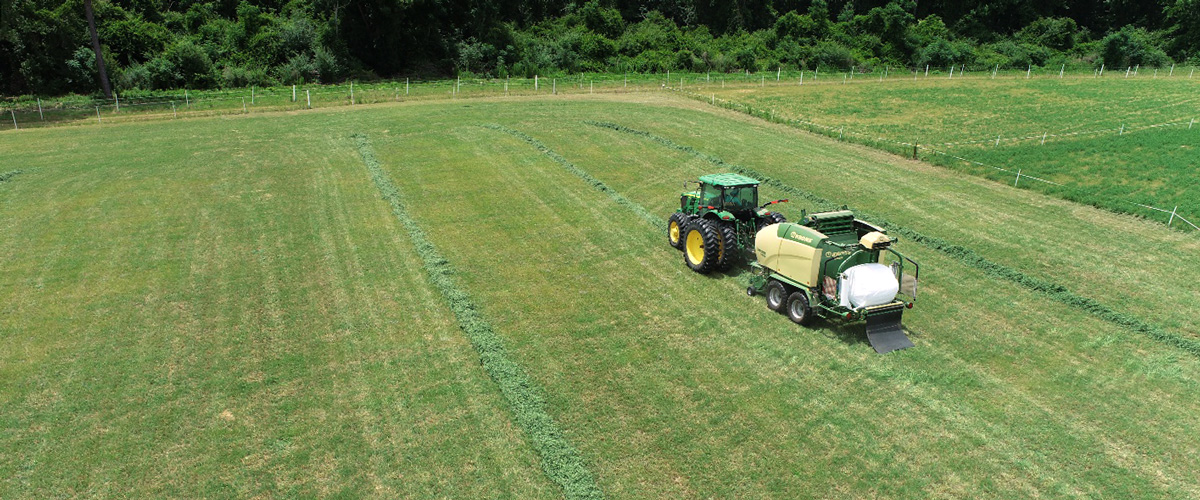
Baled silage, or “baleage,” is an excellent method for forage harvest, storage, and feed efficiency. This publication focuses on common questions about baleage. Together with UGA Extension Bulletin 1532, Baleage Production and Use, this information will help producers better understand and use baleage. For more information on forage management, please contact your local county Extension office.
Common Questions About Baleage
Why Should I Consider Making Baleage?
Baled silage allows forage to be harvested at higher whole-plant moisture levels than what is needed for dry hay. Baleage is ideal for spring cuttings of annual and perennial forages, when seasonally frequent rainfall makes it difficult to properly cure dry hay. Many producers who want to harvest small grain crops with high nutritive value have found baleage to be a good fit for their operations.
What Happens During the Baleage Fermentation and Storage (Ensiling) Process?
When moist forage (40% to 60% moisture) is baled and wrapped in plastic, respiration and microbial activity inside the plastic quickly use up the available oxygen, creating an anaerobic environment. Anaerobic microorganisms on plant surfaces then ferment some of the carbohydrates in the forage to lactic acid. The accumulation of lactic acid lowers the pH of the bale and inhibits the growth of detrimental microorganisms. Although this process consumes some dry matter and digestible energy (mainly water-soluble carbohydrates), these losses are small compared to the dry-matter losses that result from raking, tedding, baling, and storing round bales as hay.
What Equipment Will I Need?
A baleage system requires much the same equipment as a conventional hay system, with the addition of a wrapper and plastic. The minimum requirements are a mower, a rake, a baler capable of baling wet forage, a tractor with sufficient horsepower to carry these bales safely, a bale spear, and a wrapper. Some balers have a chopping mechanism that can increase bale density and reduce particle size for ease in mixing rations. Cutting the forage with knives theoretically should improve fermentation, because it increases density and provides microbes with greater access to carbohydrates in the forage. Bale spears are inexpensive ways of moving the bales prior to wrapping and just before feeding. Bale squeezes are more expensive, but are required to move bales already wrapped in plastic. Bale wrappers range in cost from $6,000 to $25,000 or more and differ considerably in labor and equipment requirements. Alternatively, producers can work with a custom bale-wrapping operator or rent a wrapper locally.
What Should I Use to Mow?
Mower-conditioners are the most popular and easiest-to-use mowing implement for the baleage system. Mower-conditioners crush the stems, which dry faster and provide a more conducive environment for microbial growth. The two most common types of conditioners are impellers and rollers or crimpers. Impellers work better for most grasses, while crimpers are preferred for legumes and thick-stemmed summer annual grasses. Although mower-conditioners are ideal, other types of mowers also can be used successfully.
When Do I Cut?
Cut the forage crop at the maturity stage that combines yields and nutritive value sufficient for your feeding requirements, similarly to hay. In general, cut legumes at 10% bloom and grasses at the boot stage or just as the head emerges. Ideally, rye and triticale should be cut no later than the boot stage. In general, early-maturity forage has higher soluble carbohydrate -, essential for proper ensiling. Conversely, overmature forages will not ferment well because they have lower soluble carbohydrate content and their coarse, stemmy nature traps more oxygen in bales.
Can My Round Baler Handle High-Moisture Hay?
Some modern variable-chamber balers are capable of baling wet forage into a dense package. However, special silage models are recommended because they are specifically designed to bale wet forage. Silage balers have modifications such as scrapers on the belts and rollers to prevent buildup of material, and they have heavy-duty bearings to help handle the increase in bale weight. Several baler manufacturers offer silage kits that can be added to older balers to enable them to handle baleage.
When Should I Bale?
Bale when moisture content reaches 60%. The time required to reach this moisture level will vary from hours to more than a day after cutting, depending on drying conditions. Baling at the proper moisture content is a key to success in producing baleage. Baleage can be made between 40% and 60% moisture, but fermentation is best when whole plant moisture is 50% to 60%. Forage containing less than 40% or more than 65% moisture should not be baled for silage to avoid excessive molding or spoilage.
Baling above 65% moisture increases the chance of undesirable butyric acid fermentation by Clostridia bacteria. Producing bales with too much moisture also reduces forage nutritive value. Forage with less than 40% moisture will not ferment well but can still be good feed as long as anaerobic conditions are maintained. However, baling with low moisture reduces fermentation and increases mold production, which greatly increases storage losses.
How Do I Determine the Proper Moisture Content of My Forage?
- Perform a “dish rag” test. Take a handful of forage and wring it out as one would wring out a dishrag. If moisture can be out squeezed out of the forage, it is generally above the 65% moisture range.
- Use a commercially available tester. These are less accurate than forced-air dryer or microwave methods. Obtain at least three moisture readings to create an average value. Commercial testing equipment can be costly, and moisture testers for hay are not calibrated for the moisture content of baleage.
- Use a Koster moisture tester. These are heated, forced-air dryers that are used in silage production to dry down the forage. The Koster system has a scale to measure weights, but it takes longer than a microwave moisture test.
- Determine whether your silage baler can be equipped with sensors that provide a continuous readout of moisture content while the bale is formed.
- Use a microwave and follow the method below, adapted from the book Southern Forages (Ball et al., 2007, p. 303): Measuring the Moisture Content of Forage Using a Microwave Oven
-
- Chop fresh forage into short lengths (< 1 in.) for ease of handling and uniform drying.
- Weigh out at least 100 g (3.5 oz) of chopped forage. You will need scales capable of measuring small quantities, such as postal scales (available at office supply stores).
- Spread forage thinly on a microwave-safe dish and place into microwave. A cup of water placed in the microwave beside the sample will help prevent the sample from igniting once dry.
- Heat for 1–2 min and reweigh.
- If forage is not completely dry, shake and redistribute the sample, and repeat the heating cycle until the sample reaches a stable weight. If charring occurs, use the previous weight. (Microwaves vary considerably in drying capacity. It is better to dry for short intervals and reweigh until the last two weights are constant, rather than run the risk of burning the sample and damaging the oven.)
- Calculate moisture content using the following equation:
% Moisture Content = (W1- W2) / W1
where W1 = weight of forage before heating; W2 = weights of forage after heating - Dry matter (DM) is the percentage of forage that is not water. DM equals 100% minus the % moisture content.
How Should I Make the Bales?
A slow ground speed during baling helps make tight, dense bales that are less likely to spoil. Net wrap is helpful in making baleage because it prevents the stems from puncturing the plastic. Plastic twine is acceptable but avoid treated sisal twine since the oils applied during the manufacturing process often degrade the plastic film and can result in large storage losses.
How Much Plastic Needs to Be Applied?
Six layers of plastic provides adequate oxygen exclusion for baleage and gives protection from punctures, though research has shown that four layers is adequate for short-term storage. Always ensure that the tension of the wrap (tacky side toward bale) keeps the film stretched uniformly over the bales. Do not apply too little plastic or oxygen will penetrate the bale and cause spoilage, mold growth, and feed losses.
For an individual bale wrapper, ensure that two layers of wrap are applied during each full rotation of the bale and that there is a 50% overlap with successive layers.
For an in-line bale wrapper, overlapping layers should be spaced no more than 5 in. apart if using a 30 in. roll (30 in./6 layers = 5 in. between edges of layers). When nonuniform bales are wrapped with an in-line wrapper, it may be helpful to apply extra plastic at the joints. The change in bale size makes it difficult for the plastic to seal, allowing oxygen infiltration and mold growth.
How Many Bales Can Be Wrapped per Hour?
Using an individual bale wrapper, experienced workers can wrap 25 or more bales per hour. This number can be doubled with an in-line wrapper.
How Much Does It Cost?
Plastic costs will vary but generally are between $90 and $100 per roll. Each roll will cover 20 to 25 bales (applying six layers). Based on these prices, the approximate cost per bale is $4 to $5. The total cost of baleage per ton of dry matter (DM) is highly dependent upon the type of wrapper used—wrapper costs vary, and the type of wrapper determines the amount of labor and plastic that will be required. In-line wrappers usually are less labor-intensive and can use less plastic than models that wrap bales individually.
What if I Feed a Molded Bale?
Even in good baleage, some bales develop a surface white mold. This usually occurs on the flat ends of bales of different sizes in in-line-wrapped forage and around previously undetected pinholes in the plastic. This type of mold rarely penetrates more than an inch into the bale. The animal usually eats around or even discards this portion. Even if ingested, this type of mold should not significantly harm the animal.
However, if red, blue, or green molds are present, exercise caution before feeding. While mold color is not a definitive way to identify toxic organisms, the presence of red, blue, and/or green molds is an indication that fermentation was poor or that oxygen has encroached into the bale and those bales should not be fed. In these cases, you may need to test for mycotoxins. Consult your local county Extension agent for more information on testing for mycotoxins.
Should I Be Concerned About Botulism?
Cattle getting botulism poisoning from baleage is not common and can be prevented. Botulism toxicity is caused by the excessive growth of Clostridium botulinum bacteria in haylage that has been baled too wet (> 60% moisture) and whose pH is not low enough to prevent clostridial growth. A baleage pH of 5.0 or below indicates good fermentation and low probability of clostridial growth.
Clostridium bacteria are common in soil, manure, and in the carcasses of decaying animals. Clostridial fermentation is not proof of botulism, as there are several strains other than botulinum. Forage can become contaminated during raking and baling from manure applications close to harvest and from dead animals that get trapped in the baled forage.
The risk of botulism toxicity from baleage is minimized by baling at less than 60% moisture, using at least four layers of plastic, and preventing puncture damage to plastic during storage. Baleage that has undergone clostridial fermentation will have high moisture (usually above 70%), high ammonia content (> 15% of total N), elevated butyric acid (> 1% of dry matter), and usually has elevated ash content from soil contamination (> 11%). Failure to maintain anaerobic conditions also has been associated with botulism in actual case studies.
To determine if clostridial fermentation has occurred, have a certified laboratory analyze a sample of the forage to determine the moisture, ash content, pH, concentrations of lactic and butyric acid, and ammonia-N. A specific test for the botulinum toxin also is available.
Should I Apply Additives?
Commercial additives for baleage vary widely in their composition, but generally contain enzymes and inoculants to assist in fermentation. Excellent baleage can be made without the use of commercial additives. Inoculants that contain fermenting bacteria provide insurance that adequate microbial numbers are present on the moist forage at baling. Inoculants may be especially helpful with early-spring and late-fall baleage, when cool temperatures limit the number of natural fermenters present on forage surfaces.
Inoculants contain lactic acid bacteria (LAB) that may be homofermenters (produce only lactic acid) or heterofermenters (produce lactic plus acetic acid). Lactic-acid formers increase the speed of fermentation by supporting higher lactic acid formation. The production of acetic acid by heterofermenters improves the stability of silage during feedout. Inoculants are best applied in liquid form, usually by applicators mounted on the baler.
How Soon Should I Wrap the Bales?
Ideally, wrap forage immediately or within 12 hr of baling. Delays between baling and wrapping lowers the feed’s nutritive value by allowing undesirable microbial activity and excessive heating.
Where Should I Wrap the Bales?
Wrapping at the storage site minimizes the handling of wrapped bales and reduces the potential for damaging the plastic. Store bales on a well-drained sod, away from trees or weeds that might harbor rodents and insects that attract birds and lead to plastic damage. Avoid locations with excessively coarse stubble that may cause small punctures. Using six layers of plastic will help protect the baleage from punctures. Patch any small holes in the plastic using a repair tape treated to resist degradation from UV light.
What Kind of Wrap Should Be Used?
The plastic wrap used in making baleage is a polyethylene plastic film that is pre-stretched 50% to 70% by the wrapper as it is applied to the bale. The plastic must be able to withstand the local environmental conditions such as UV radiation and changes in ambient air temperature. Tear strength and tack (stickiness) may vary among brands of wrap. Plastic film may be white or black. White plastic is most common in the Southeast region since it reflects sunlight better and reduces solar heating of the plastic.
What Type of Wrapper is Best?
Three major types of wrappers are available, and all can produce good baleage. The main types are (a) platform, (b) swinging arm, and (c) in-line.
Platform wrappers simultaneously rotate and revolve the bale on a platform to feed plastic from a stationary roll.
Swinging-arm wrappers have rollers that open to enclose and pick up the bale before wrapping. The plastic roll swings around the bale on an arm. More recently, integrated baler-wrapper designs have become available that wrap the bale just after it is formed.
In-line wrappers place bales end-to-end in a row while dispensing plastic from rollers that travel around the bale. In-line wrappers are popular because of their quick wrapping rates, reduced plastic consumption, and ease of use. Many in-line wrappers have automatic wrapping features with remote control options that allow the producer to operate the machine from the tractor, thereby reducing labor requirements. These wrappers are not recommended for producers who cannot continuously feed out the baleage at a rate of 1–2 bales per day. Once the tube is opened, the bales need to be fed continuously to prevent spoilage.
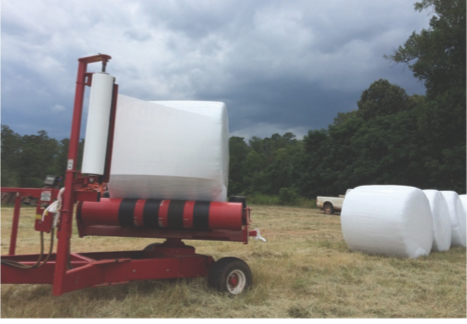
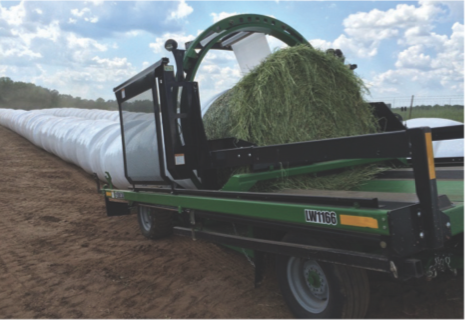
Is Baleage Higher in Quality (Nutritive Value)?
When comparing properly ensiled baleage to properly cured dry hay, the nutritive value of baleage is higher because of decreased losses from harvest and storage. The process of ensiling also will metabolize excess nitrate, lessening the chance for toxicity. In addition, ensiling will detoxify the toxins associated with buttercup (Ranunculs spp.). Ultimately, stage of maturity at harvest determines nutritive value. Therefore, the nutritive value of forage when it’s cut is the greatest determining factor on the baleage quality. The ensiling process does not improve the nutritive value of the forage but helps protect the nutrients that are already there.
How Soon After Wrapping Can I Feed Baleage?
Baleage can be fed any time after wrapping but requires at least 4 weeks to achieve a stable pH from fermentation. Well-fermented baleage will be more stable (less likely to be microbially degraded) when fed. Opening up an in-line tube of bales before it has reached a stable pH will increase losses because the end bales have been re-exposed to oxygen.
How Long Can Baleage be Stored Before Feeding?
In general, forages baled at 40% to 60% moisture will maintain feed value for about 12 months, as long as the integrity of the plastic is maintained. However, even where the forage was baled at the appropriate moisture level and the plastic is intact, it is good practice to feed baleage bales within 9 months.
What Kind of Feeding System Do I Need to Use to Minimize Losses?
Use a ring feeder, cone-type ring feeder, or elevated bale wagon to minimize losses during feeding. Losses can reach 50% when feeding without using one of these devices. When feeding whole baleage packages to any species, it is best to feed enough animals that they will eat the entire bale within 2 to 3 days. Baleage also may be integrated into rations by grinding and mixing.
What Animals Can I Feed Baleage To?
Traditionally, baleage has been fed to beef and dairy cattle, but it also can be fed to sheep and goats. Baleage generally is not recommended for horses because of surface mold and—especially—their sensitivity to Closteridium bacteria, which causes botulism poisoning. To ensure the most efficient use of the nutritive value in a baleage bale, it is important to match the bale’s nutritive value to the animals’ economic productivity. Baleage can and should be tested for nutrient levels in the same manner as dry hay.
What Should I Do With the Used Plastic?
Because the plastic for making baleage can be used only once, the plastic must be disposed of properly to avoid an environmental problem. Currently, there are no standard policies for collection and disposal of used baleage plastic beyond deposition in landfills. In the future, used plastic may be collected for recycling, but there are no active recyclers of baleage plastic in Georgia at this time. Check with your local government or division of solid waste on applicable statutes in your area for disposal or recycling.
Can I Wrap Dry Hay as an Alternative to Inside Storage?
Some producers who have limited inside space for storing dry hay rolls have successfully wrapped dry hay for outside storage. Typically, all that’s needed is two layers of plastic with about a 20% overlap at the edges—just enough plastic to cover the bale. For best results, allow hay to go through the sweat period (typically 1 to 2 weeks) before wrapping.
Conclusion
There are many benefits to including baleage technology into your forage production system. Harvesting the forage as baleage allows for a more timely harvest, improves leaf retention, and reduces losses of dry matter or nutritive value. However, baleage does have additional costs including a wrapper, plastic, and plastic disposal. Producers need to weigh the benefits, challenges, and costs before adopting baleage on their farm. For more detailed information on baleage production, please refer to UGA Extension Bulletin B 1532 Baleage Production and Use, as this information will help producers better understand and use baleage. For more information on forage management, please contact your local county Extension office.
Reference
Ball, D. M., Hoveland, C. S., & Lacefield, G. D. (2007). Southern forages: Modern concepts for forage crop management (4th ed.). International Plant Nutrition Institute.
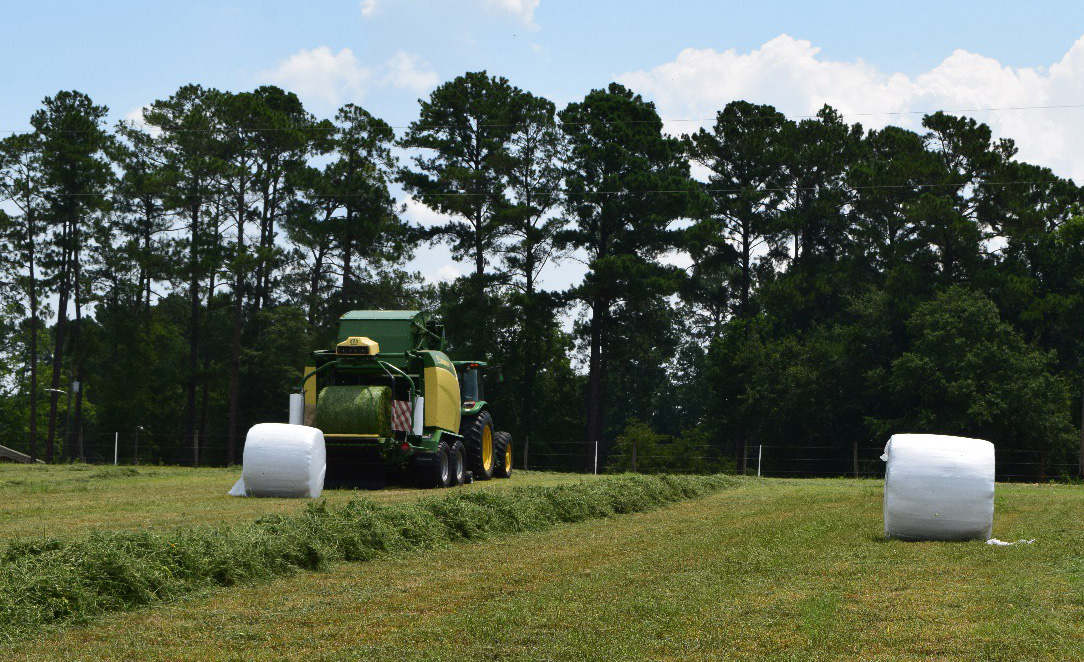
Additional authors from the University of Kentucky: Jimmy C. Henning, Chris Teutsch, Ray Smith, and Brandon Sears. The authors acknowledge the contributions of Dennis Hancock, former Extension forage specialist for the University of Georgia, to previous versions of this publication.
Status and Revision History
Published on Feb 27, 2019
In Review for Major Revisions on Aug 25, 2023
Published with Major Revisions on Aug 28, 2023