What is a recall?
The U.S. Food and Drug Administration (FDA) defines a recall as actions taken by a firm to remove a product from the market. A well-designed recall plan will help to effectively locate the recalled product, remove it from the market, and locate the source of error in the product. It serves a guide for the company to follow if a situation requiring a recall presents itself. Recalls can be conducted on a firm’s own initiative, by FDA request, or by FDA order under statutory authority. If a situation requiring a recall does present itself, it is in the company’s best interest to recall a product before an outbreak occurs.
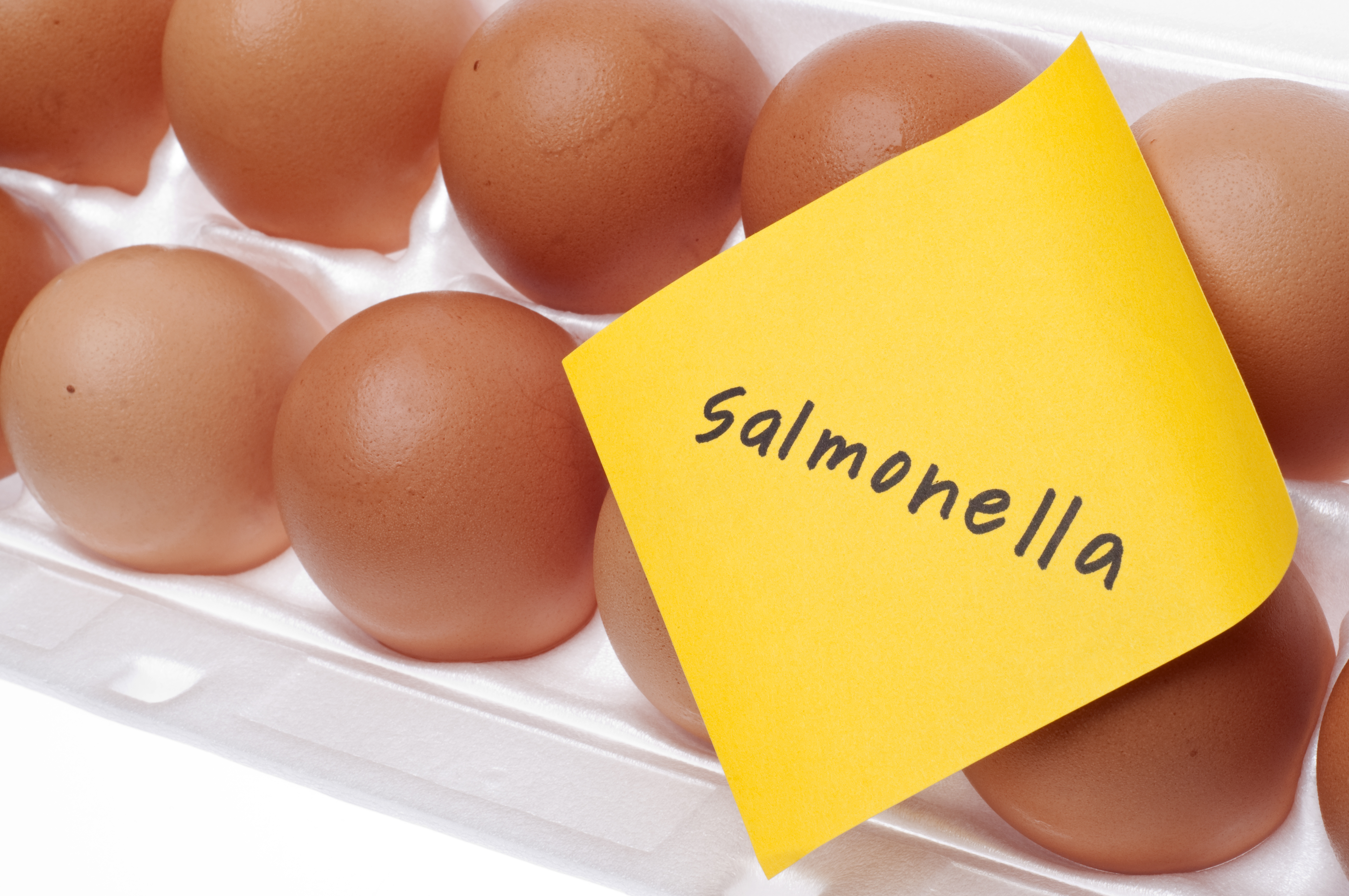
Who handles recalls?
The FDA and the Food Safety Inspection Services (FSIS) within the U.S. Department of Agriculture (USDA) are the government agencies responsible for the safety of the food supply in the U.S.4 The FSIS is responsible for the safety of the meat and poultry industry (including catfish) and FDA ensures the safety of all other foods. If the company chooses not to do a product recall then FSIS or the FDA will have no choice but to remove the product or halt the processing of that food product. Your company should consider its type of food products and determine which agency you would work with in the case of a recall. This guide will focus more on the strategies for working with the FDA. According to your location, you are assigned a local FDA district recall coordinator with whom you will work closely in the case of a recall.
Developing a recall plan
Recall plans require careful attention and forethought. They are comprised of several parts, which must all be able to work together during a critical time. Because a recall plan can quickly become complicated, it is best to develop it in a series of steps that build on each other. The following pages will provide an outline of steps that can be followed to develop a useful recall plan.
Assembling a recall team
When you begin to consider how a recall in your company would be handled, you may find yourself forming a long list of responsibilities that span a variety of positions. If a recall situation does occur, it is important to know who will be in charge of overseeing each responsibility. Thus, it is helpful to begin making your recall plan by forming a list of specific people for a recall team.
A recall team is a group of trained individuals who can effectively execute the procedures of a product recall when needed. The team aspect is important because these individuals must be able to work together to execute an effective recall. Team members should represent a variety of departments within the company and each should act as a leader within his or her department. There should be a manager or coordinator of the recall team who is responsible for managing, maintaining and altering the recall plan when necessary.1 The recall manager can recommend a recall but the final decision is up to management.
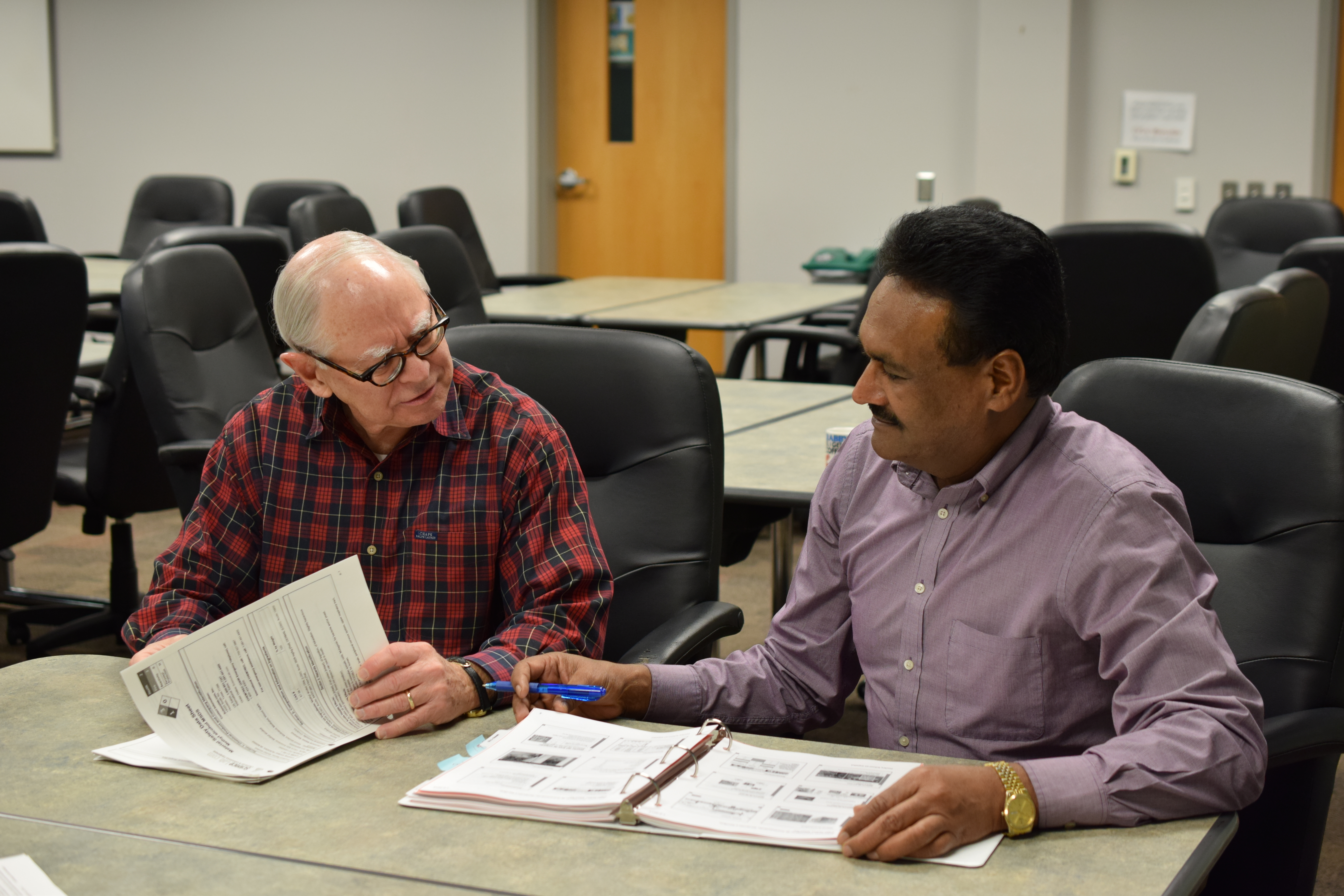
When a product is recalled, the team evaluates the severity of the recall and determines what actions need to be made. Once the decision to recall a product is finalized, the team should determine the avenue of communication and who is responsible for managing the recalled products. The severity of the recall will also affect how the announcement is made. Members of the recall team should be representatives from departments within the company including, but not limited to, quality assurance, product development, shipping and distribution, and accounting.4 The recall manager should be able to contact the recall team members immediately in case of an emergency. The recall manager also serves as the liaison between the recall team and the company’s managers.
The local FDA district recall coordinator should be listed as part of your recall team. While this agent does not work directly in your company, they should be among the first to be notified of a recall and will be play an active role through the process. You can find the contact information for your FDA district coordinator at www.fda.gov/Safety/Recalls/IndustryGuidance/ucm129334.htm.
Listed below are responsibilities that should be delegated among individuals on the recall team. An individual may have more than one responsibility.
- Management
- Accounting
- Consumer relations
- Customer service
- Information and technology
- Legal counsel
- Marketing
- Operations
- Production
- Purchasing
- Quality assurance
- Sales
- Maintenance
- Records Management
- Regulatory affairs
- Sanitation
- Distribution and supply
*See Appendix A for the recall team contact information worksheet.
Determining when to issue a recall
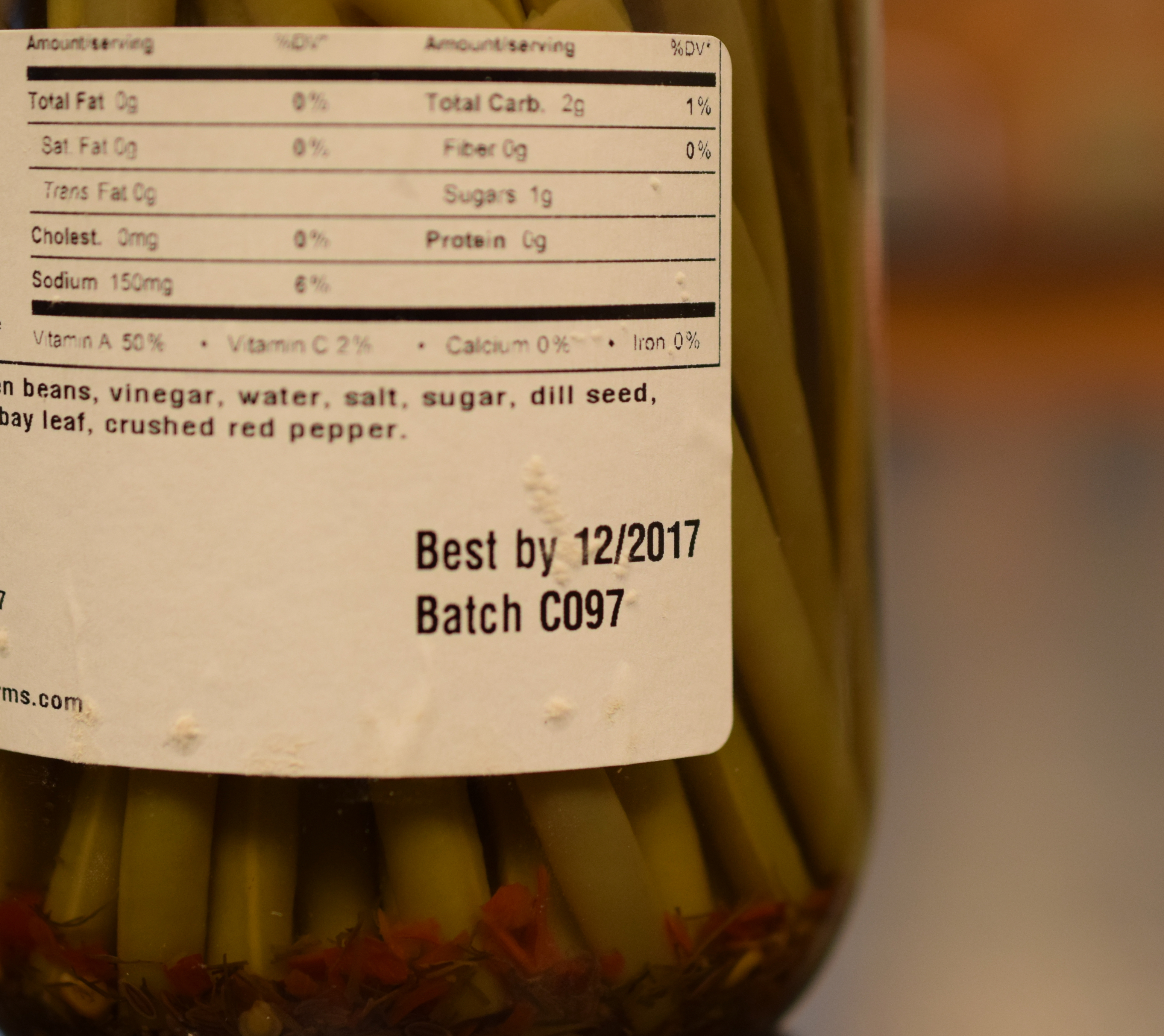
Once you have established who will be in charge of carrying out a recall, you should form a set of guidelines to help them decide when to enact a recall. The parameters for issuing a recall will most likely be a bit different for every company depending on its production.
Figure 1 provides a visual of the paths that can be taken depending on how the recall process begins.
-
A recall can begin when testing/monitoring within the company reveals that a product is adulterated, misbranded, contaminated, or defective. From that point, the problem can be taken directly to management, who will decide what action to take depending on whether he product has left the facility and activate the recall accordingly.
-
If a government agency requests that a product be recalled, the product can either be tested to confirm or deny the problem, or management can decide to activate the recall immediately.
-
If your company receives enough customer complaints about a product, it may be necessary to test the product, and management will decide if it is necessary to activate a recall.
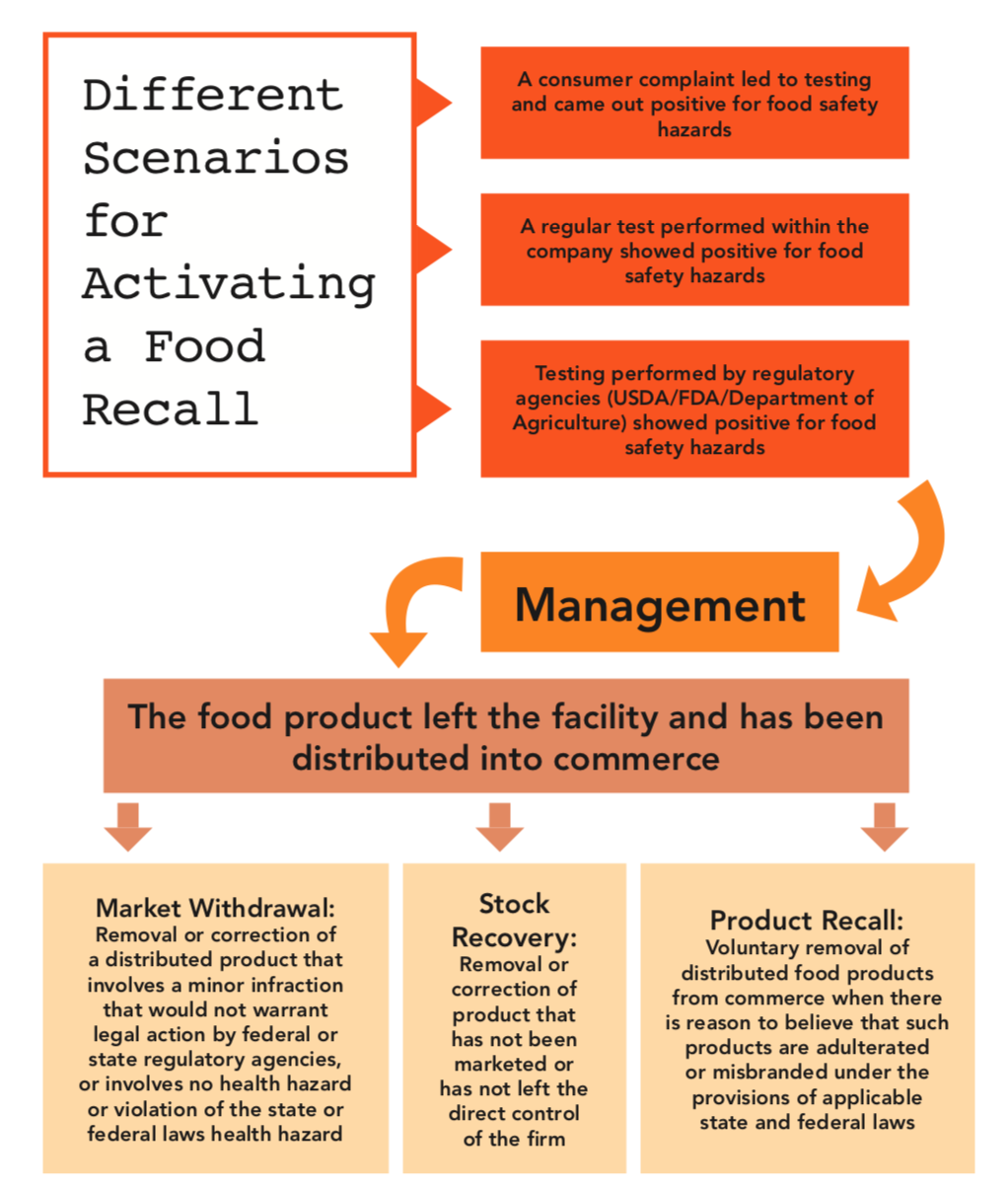
Figure 1. Diagrammatic representation of a food recall activation scenario showing different recall types (e.g., stock recovery, market withdrawal, and recall).
Customer Complaints
If your company receives feedback on a regular basis, it is likely that some customer complaints will be a regular occurrence. For the benefit of your recall plan, you should keep a record of the complaints, and determine a set number of complaints that is considered normal. Then, if the number of complaints over a period exceeds the “normal” amount, you will know to begin testing for problems and considering a recall.
Ensuring traceability of products
The success of a product recall will largely depend on how accurately the company’s records can identify specific products by parameters such as model numbers, serial numbers, and batch numbers. It is vital to keep records (invoices, bills of sale, shipping documentation, etc.) on file to aid in tracing all of the raw ingredients included in the product. Product traceability should start with the supply of raw materials and progress through the production and distribution system. It is critical to have an effective document control system in place in the event that a recall of a product is needed. Management should be able to identify products by a batch number, serial number, lot number, and/or expiration date. A practical and efficient tracking and identification records system must be established before products are distributed. It is best to have two or more methods of identifying the product. Recorded information that should be provided includes:
-
Product identification
-
Production records
-
Microbial/safety testing data
-
Distribution information
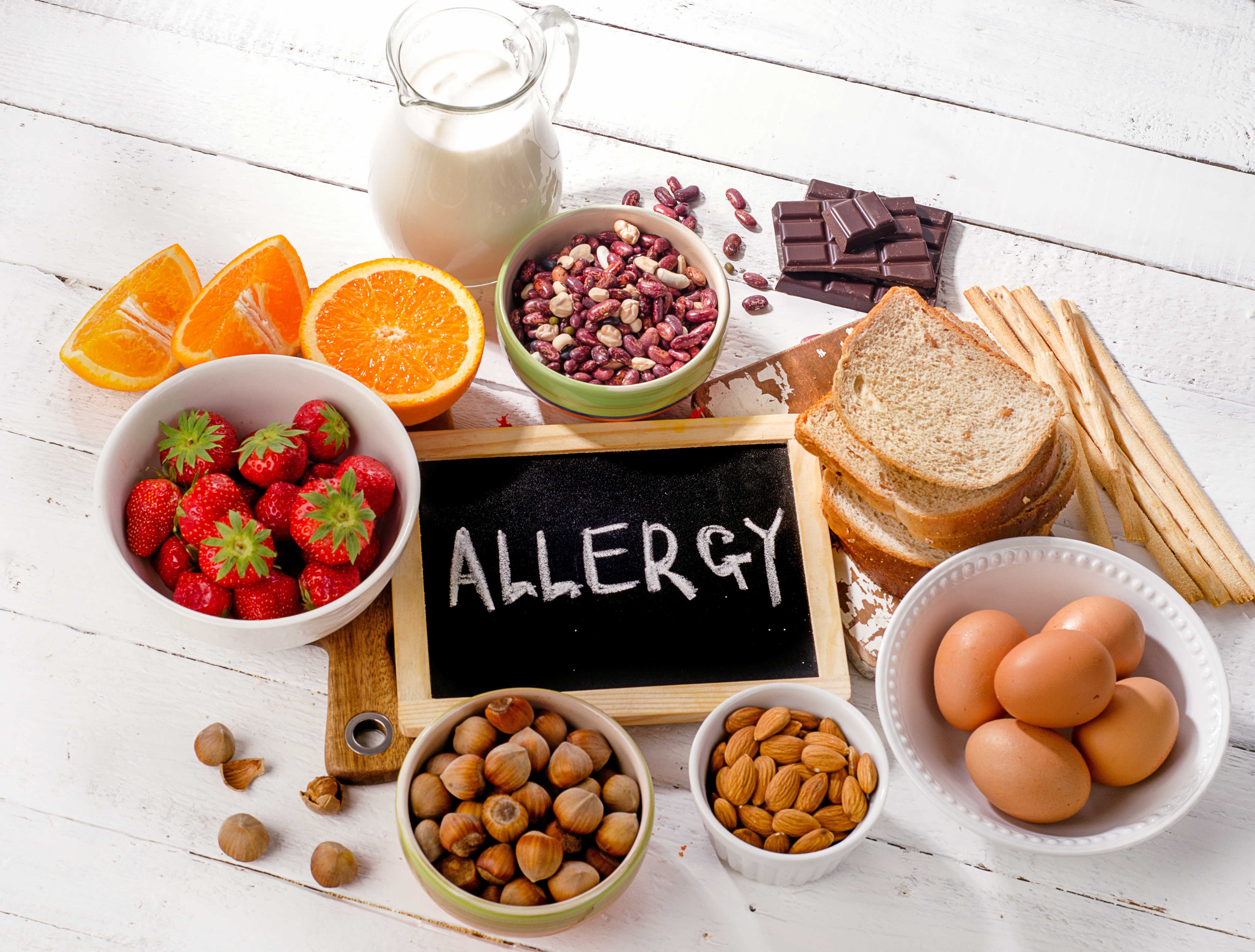
Classification of a recall
A recall plan should be developed according to the classification that the recall may fall under. When determining how to proceed with the recall, the recall coordinator should start off by evaluating the risk associated with the recall. This will allow the recall team to classify the recall and determine its urgency. You can find a list of the risk classifications as stated by the USDA and FDA and examples of each below.1
Class I:
-
There is a high probability that exposure or consumption of the product will cause adverse health consequences or death
-
Clostridium botulinum toxin is in the food
-
An allergen is incorrectly labeled
Class II:
-
Use of or exposure to a product may put the consumer at risk of temporary reversible adverse health consequences
-
Presence of undeclared allergens like milk, soy that are associated with mild human reactions
-
Improper seal on a product causing potentially harmful mold or bacteria growth
Class III:
-
The product is defective but is not likely to pose a risk of health consequences
-
Damaged packaging that does not compromise food safety
- Failure to label an ingredient that is not a known allergen
Recall communication
Any time a recall is being made, it is recommended that you begin communication with your local FDA district recall coordinator immediately. You will need to provide them with a recall submission containing various details about the recall. While it is best to have this information readily available to send to the coordinator, you should contact them as soon as possible, even if all of the information is not yet fully compiled. The sooner the FDA is notified, the more helpful they can be.
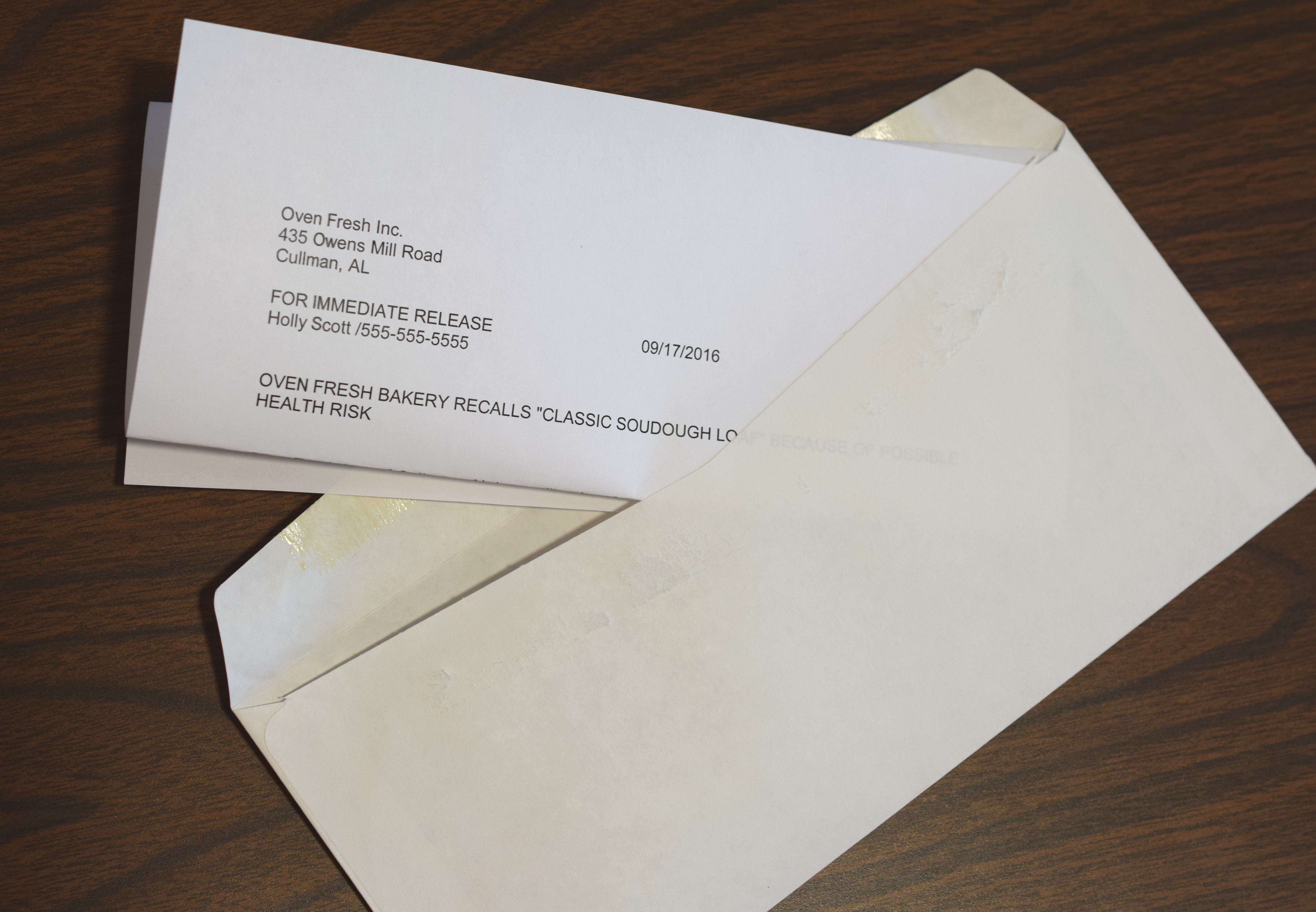
The classification of the recall will determine who else needs to be notified. Notifications during a recall must be done in a timely manner and should include appropriate regulatory agencies, the product distribution chain, and consumers, when necessary. The higher the risk and the more consumers that your product has reached, the broader the necessary distribution of recall alerts.
Once the classification is determined, a notice should be prepared to send to retailers, distribution centers, and wholesalers, which should include the following:
Identify the product by including some or all of the following:
-
Product/brand name
-
Product code
-
Package/case size
-
Package/case date code
-
Establishment number
-
Lot number/expiration date
-
Universal Product Code (UPC)
-
Risk assessment if the product is consumed
-
Reasons for recalling the product
-
Instructions for what to do with the recalled products
-
How the recipient can confirm to the recalling agency whether it has any of the product
- Contact information for further questions
Distribution level
In addition to determining the risk classification of a recall, your company should also take into consideration the distribution levels when planning recall communication. Distribution levels are classified as wholesale, retail, hotel/restaurant/institutional, and consumer users. As expected, when more levels of distribution are affected, there will be a need for more communication efforts.
- On the wholesale level, the product is distributed to a warehouse or distribution center from which it will be sold to a retailer.
- At the retail level, the retailer receives the product then sells it directly to consumers.
- “HRI level” is the term used when the product is received by hotels, restaurants, or institutional customers to be used in food service.
- Consumer level distribution cuts out any middlemen and involves the sale of the product directly to the end user from the manufacturer
Just like there are various levels of distribution, there are various levels of recall communication. Recalls can be announced via a press release through national or local news media, via a company website, personal visits, telephone, fax, or point-of-sale posters. Be sure to include contact information for all of the media outlets that you may use in your recall plan.
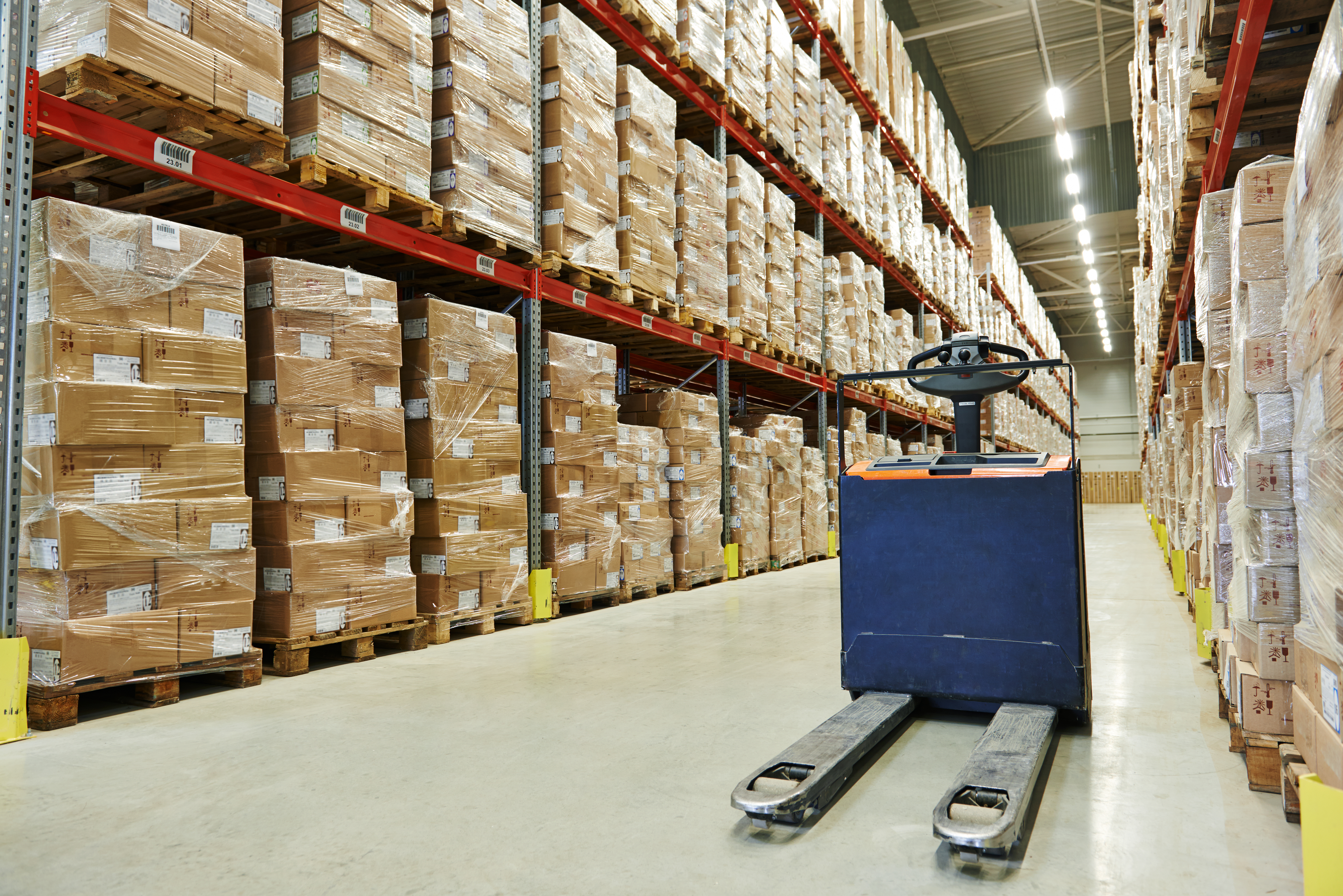
If the recall is deemed Class I, it is recommended that you alert the media immediately. Written notices should have a striking heading to indicate the level of importance. A confirmation letter should follow communication that is conducted over the telephone, email or fax to provide proof that everyone was notified.
Your recall team should discuss these options and determine which communication avenues would be best for your company according to each risk classification and distribution level. These decisions should be made and approved by management well before a recall is needed so that there is no loss of time when a recall is in action. Your recall plan should include the list of contacts with whom you will work in the case of a recall.
*Refer to Appendix B for sample recall notices and Appendix F for a FDA recall submission template.
Recall procedure
Now that you have planned who will manage a recall within your company, how you will trace recalled products and classify them by risk, and how you will communicate recall information to the public, you can culminate these elements to be used in your recall procedure. All of the parts must be planned first so that the recall procedure can run as smoothly as possible if it has to be implemented. The way that the recall procedure is carried out from company to company may vary slightly, but most will follow the general steps found in Figure 2. More information to help you with steps 10-13 will be covered next.
The general steps for carrying out a recall procedure
- Compile a list of all the distribution outlets of the product under recall.
- Notify everyone along the distribution chain through the decided communication forms.
- Send out a press release if management deems it necessary.
- Gain control of all of the recalled products.
- Verify the recall effectiveness.
- Take the appropriate corrective action (by disposal or fixing the problem).
- Terminate the recall.
- Determine the problem that necessitates a recall.
- Assemble the recall team to being working.
- Determine risk classification of the product under recall.
- Send notification of the problem to your FDA district recall coordinator.
- Identify and locate all products subject to recall according to their tracking information.
- Quarantine any affected products that are still under the company's control.
Gaining control of the recalled product
When planning your recall, it is important to make plans for how your company will get the product under its control and what to do with it next.
Removal
Removing your recalled products from the market can be fairly simple or very complicated depending on how widely the product is distributed. The best way to ensure that you can successfully remove the product is to have an effective tracking system and keep thorough records. If you have all of this information on hand, it should be simple to find the products that have left the company and regain control. Your company’s shipping and logistics personnel will be essential in formulating and executing this part of the plan.
The notifications to your distribution outlets and consumers should have included instructions to help them get return the products to you. If the products are still centrally located at a wholesaler, they can be easily collected and returned to the company. If the product has been sold to consumers, it is best to have consumers return the products to the place of purchase and then collect the products from there. Once these products have been retained, they should be segregated, detained, and clearly marked “not for sale or distribution.” Recalled products that have not yet left the company’s control should also be immediately segregated and detained in an area with clear identification that they are not for sale. While this process is being carried out, it is crucial to keep accurate records of all of the products that have been located and/or removed and their current location. The documentation should be as thorough as possible, including identification codes and exact quantities.
In some cases, management may decide that it is not necessary to actually remove all of the recalled product that has gone out to customers. Consumers who have already purchased the product must be notified of its recall, but they are left with the option to either return it for a refund or simply discard the product at their convenience. In this case, effectiveness check surveys are useful to make sure that the products that have not been removed are accounted for.
*Refer to Appendix C: A recalled product tracking worksheet is provided to help record the location of recalled products.
Product disposition
Once the products are detained, the recall team will need to decide the fate of the recalled products. It will be helpful to set guidelines for disposition of your products with hypothetical but reasonable problems specific to the products that your company produces in the recall plan. In the event of an actual recall, the problem may be unique and unexpected, but having a general idea of disposition options will still help the process run more smoothly. Your options for disposition will be limited by
the severity of the problem. Severe situations may call for the complete destruction of the product. Conversely, with an issue as simple as an omitted ingredient on the ingredient list can be relabeled and redistributed. The options for disposition of the product can be summarized by the following list:11
-
Redirection – Products are reused for a purpose other than what was originally intended, which generally excludes human consumption.
-
Destruction – It is determined that the product is unsafe for consumption and must be destroyed before disposing.
-
Recondition – Products have a safety risk that can be fixed and then allow the products to be redistributed.
Before redirecting, destroying or reconditioning the recalled products, the appropriate regulatory agencies should be contacted. It is important to gain their approval of the disposition plan before proceeding to avoid problems later on. In some cases, they may require that a representative of their agency witness the disposition or destruction.
Recall effectiveness
The records that your company keeps during the removal process will be the key to determining the effectiveness of the recall. Determining the effectiveness of the recall will allow you to verify that all of the possible recipients of the recalled products have been notified and have taken action. In order to verify this, you must examine the percentage of the number of units of affected product that have left the warehouse to the number of units that were returned or accounted for. If 100% of the recalled products are not accounted for, it may be necessary to reassess the recall strategy. The effectiveness numbers should be reported to management, who will decide if the severity of the problem necessitates revisiting the recall procedure.
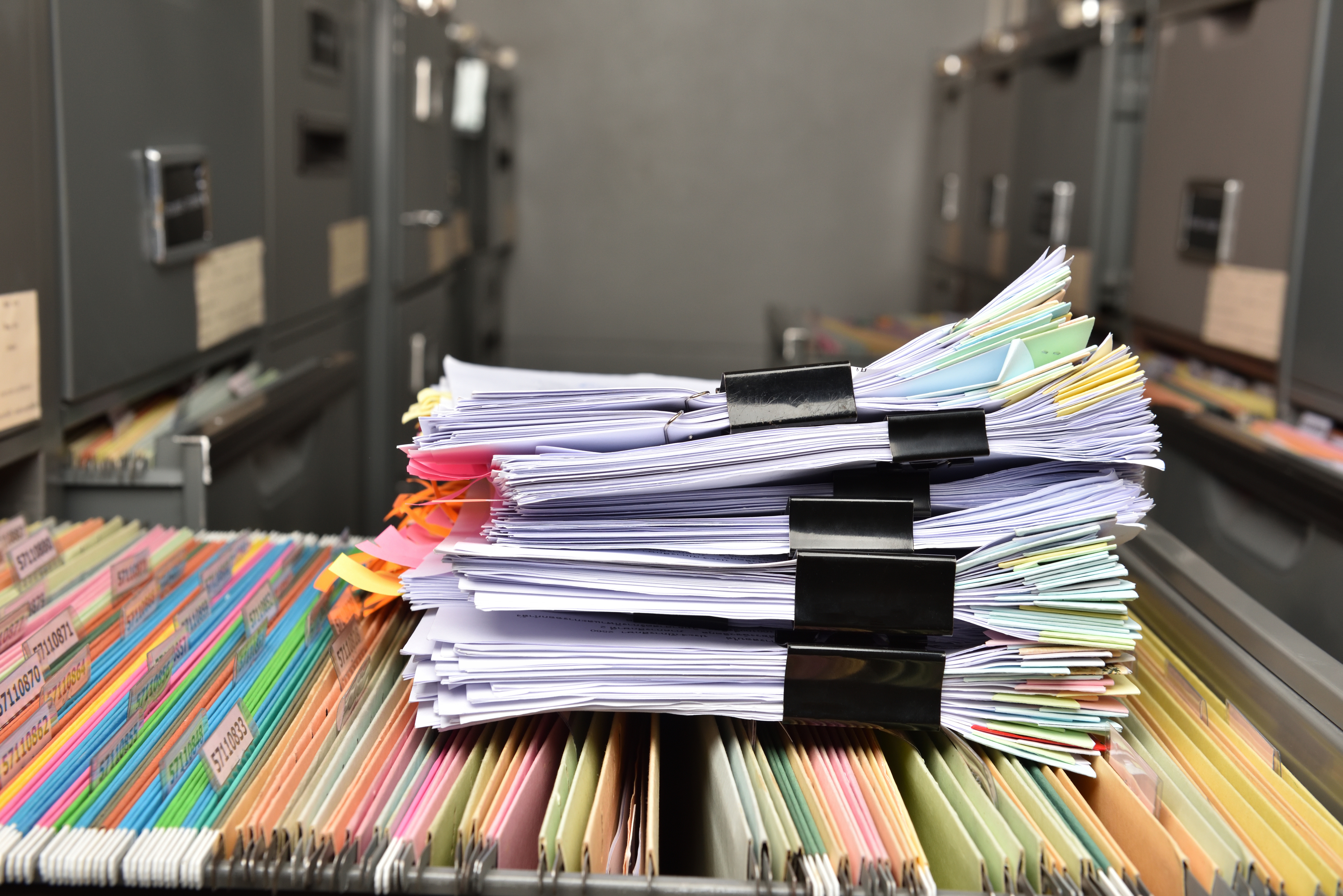
Since some recall situations do not require that the entire supply of the product be returned to the company, questionnaires can be distributed to everyone along the distribution chain to account for the recalled products. This provides another reason for keeping accurate distribution records and customer contacts.
The FDA may perform a recall audit check by contacting a percentage of your customers to ensure that your company has fulfilled the responsibilities of a recall. If the audit shows that your recall strategy was not effective, the FDA may require that you revisit the recall communication. Additionally, your district recall coordinator may request periodic status reports after a recall has been initiated. They will indicate what information should be included.
*Refer to Appendix D for a sample effectiveness check letter and questionnaire.
Reportable Food Registry for industry12
About the Reportable Food Registry (RFR)
-
The RFR is an electronic portal for industry to report when there is reasonable probability that an article of food will cause serious adverse health consequences. The RFR helps the FDA better protect public health by tracking patterns and targeting inspections. The Food and Drug Administration Amendments Act of 2007 (Pub. L.110-085), section 1005 directs the FDA to establish a Reportable Food Registry for Industry.
-
The RFR applies to all FDA-regulated categories of food and feed, except dietary supplements and infant formula.
Who should use the RFR?
-
Registered food facilities that manufacture, process, pack, or hold food for human or animal consumption in the U.S. under section 415(a) of the FD&C Act (21 U.S.C. 350d) are required to report when there is a reasonable probability that the use of, or exposure to, an article of food will cause serious adverse health consequences or death to humans or animals.
-
Federal, state, and local government officials may voluntarily use the RFR portal to report information that may come to them about reportable foods.
Where should consumers, food retailers, and food service operators report a problem with food?
- In emergencies, consumers, food retailers and food service operators should continue to call the FDA at 1-866-300-4374 or 301-796-8240. For less urgent problems, contact the FDA consumer complaint coordinator in your geographic area or see the guide to reporting problems to FDA.
What to do if the Safety Reporting Portal is not operating
- The FDA intends to post an announcement on www.fda.gov as to how to submit a reportable food report in the event that the Safety Reporting Portal is not operating. If www.fda.gov is not operating, The FDA recommends that you contact the FDA district office serving your area. If the FDA district office for your area is not listed in your local telephone directory under “U.S. Government,” call 1-888-SAFEFOOD (Monday-Friday, 8:00 a.m. to 4:00 p.m. Eastern Standard Time) or 1-888-INFO-FDA. The FDA further recommends that a report be submitted by the responsible party to the Safety Reporting Portal as soon as it resumes operation.
Recall termination
The recall team may consider termination of the recall once every effort has been made to correct the problem. This includes carrying out all of the previous steps to the best ability of the company to prevent sickness or injury form occurring as a result of the recalled product. When developing your recall plan, you should work with management and the FDA to set parameters for the acceptable effectiveness of each step. This will provide a guideline for the recall team to use when considering a recall. Management and the involved regulatory agencies should be informed and give their approval before the recall is officially terminated.
Recall simulations
Conducting mock recalls regularly is a practical way to test and work out any problems in your recall plan. A recall simulation will also allow the recall team and all involved personnel to become familiar with their responsibilities throughout the recall procedure. This gives them time to effectively communicate any concerns about the plan while the company isn’t dealing with the pressure of an actual recall. Mock recalls should be performed at least once a year and whenever there are significant changes in the structure or personnel of the company and distribution chain or changes to the plan.
Worksheets and templates
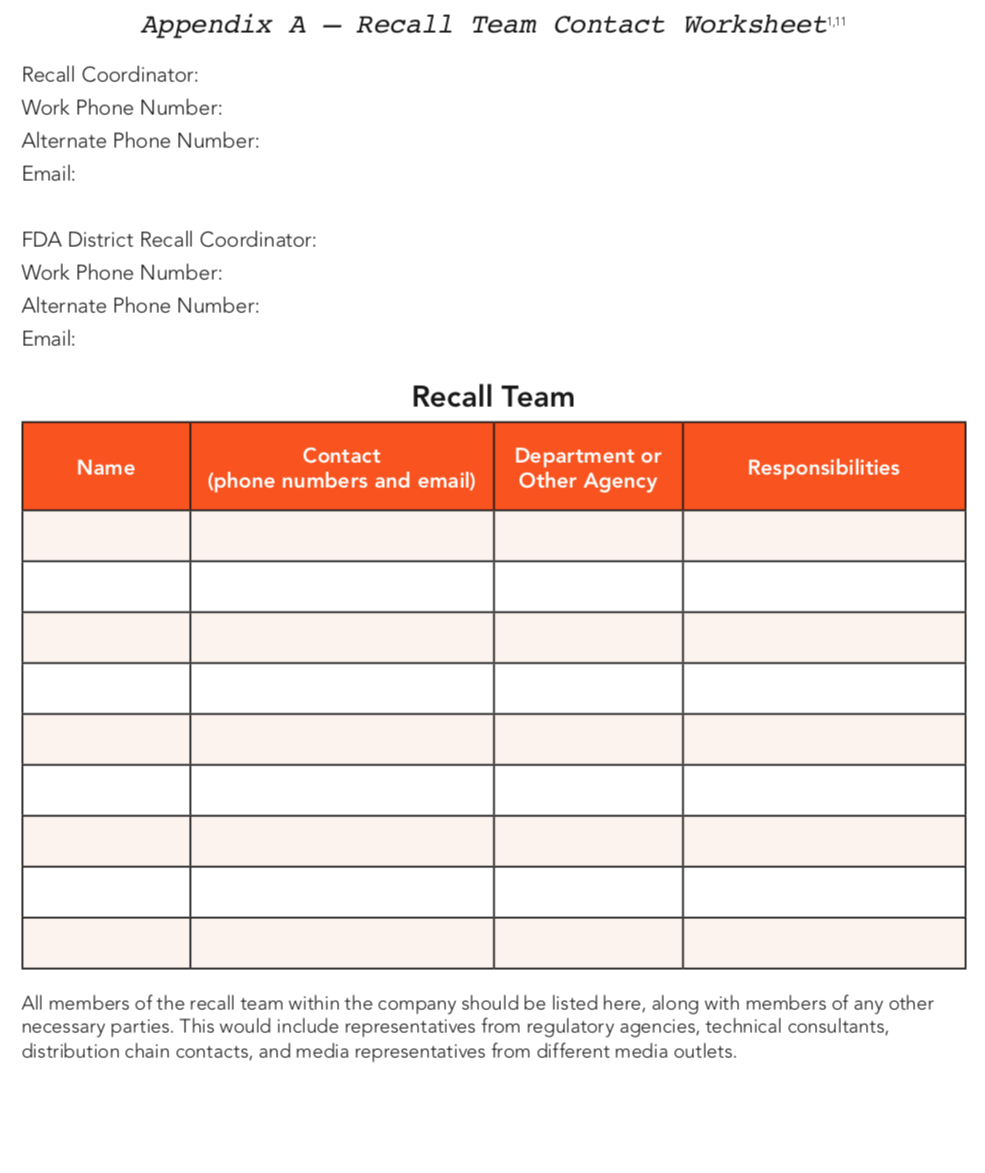
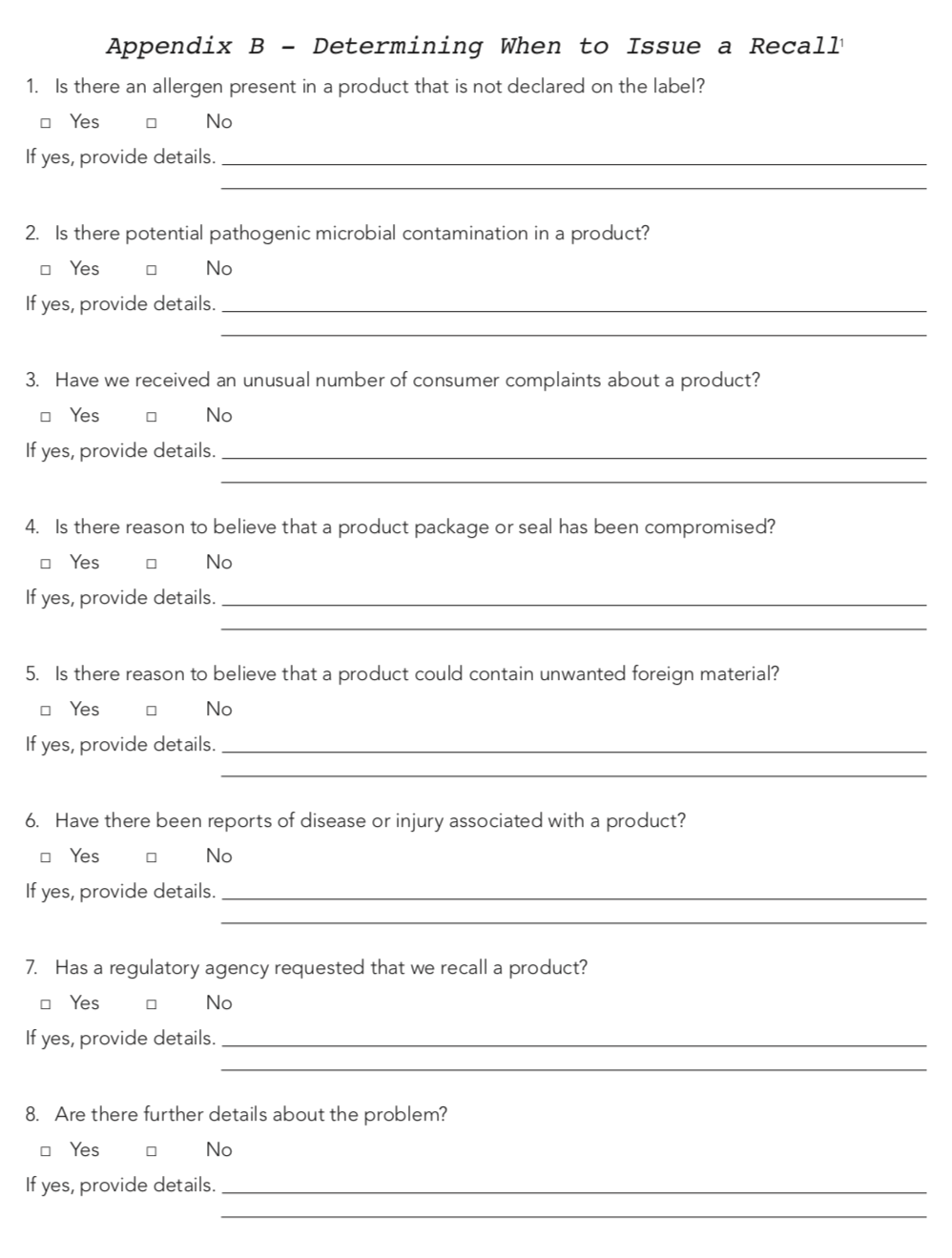
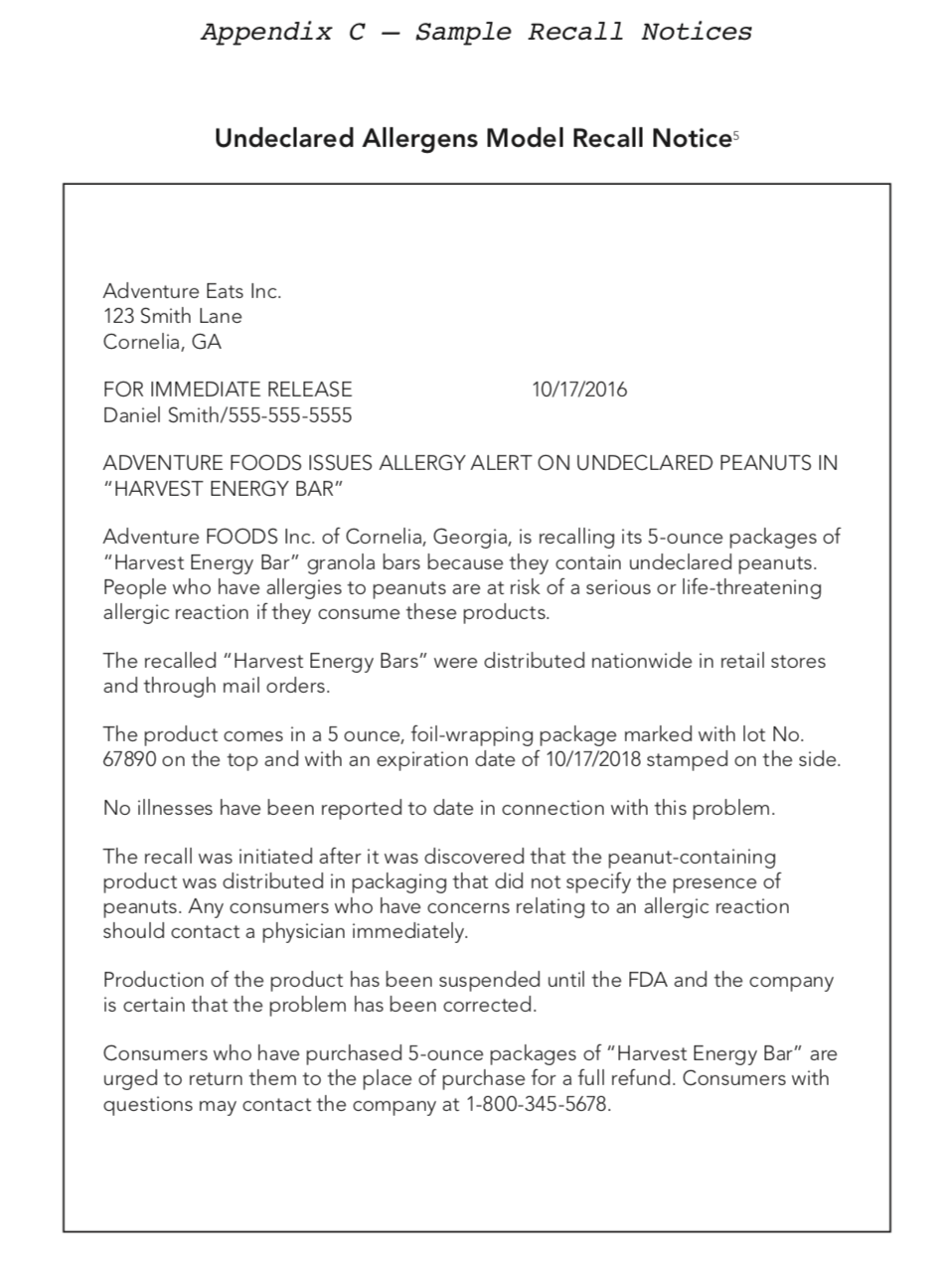
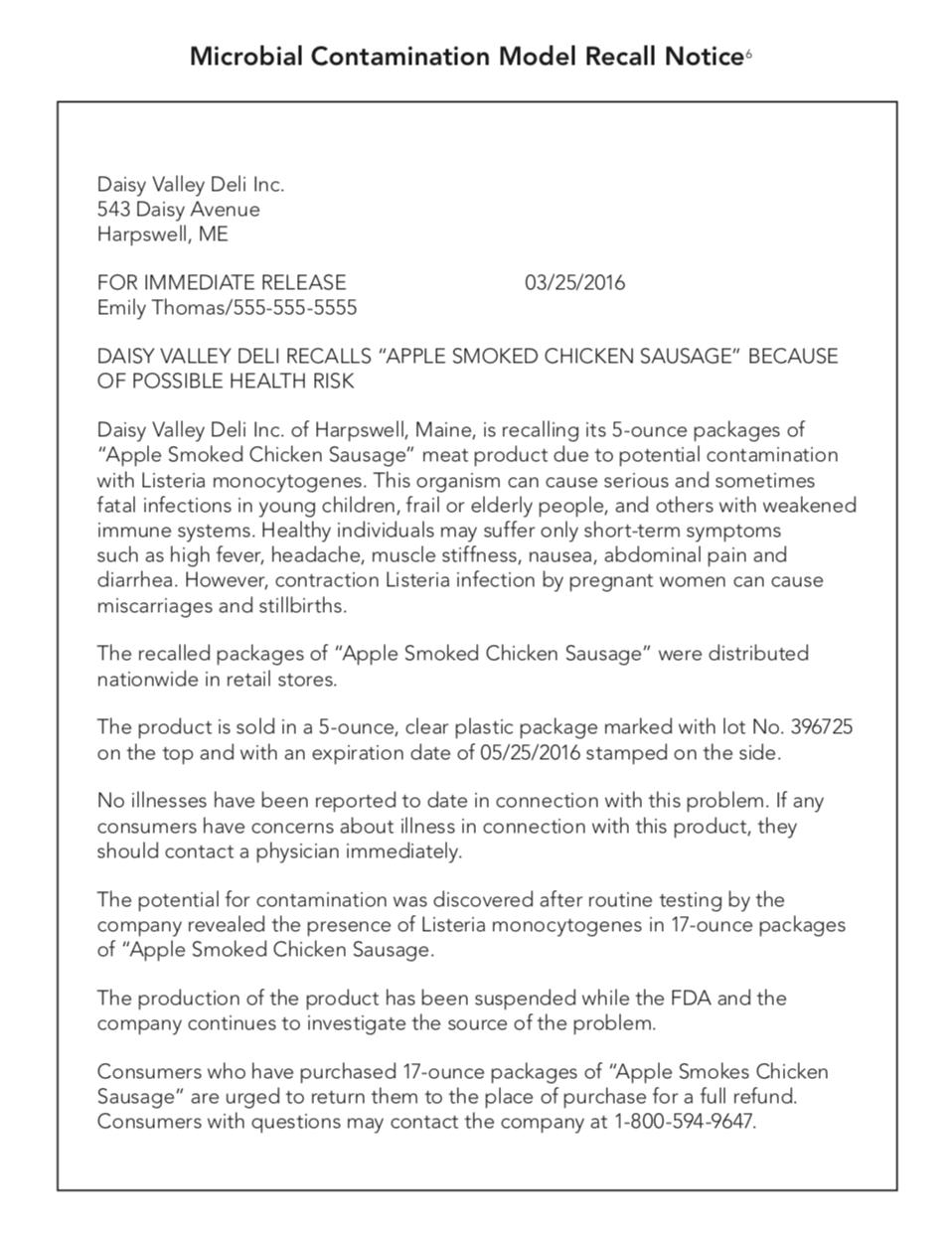
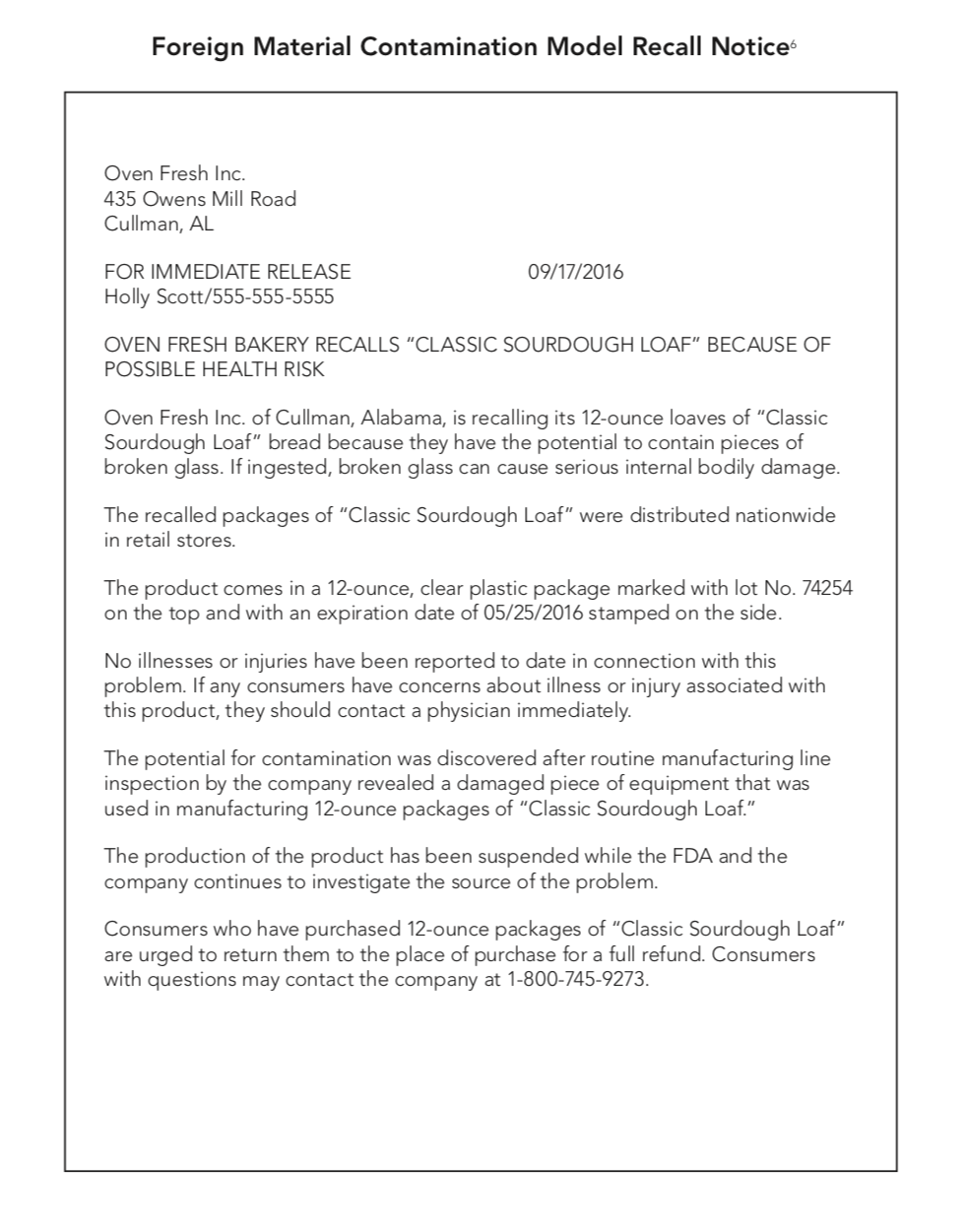
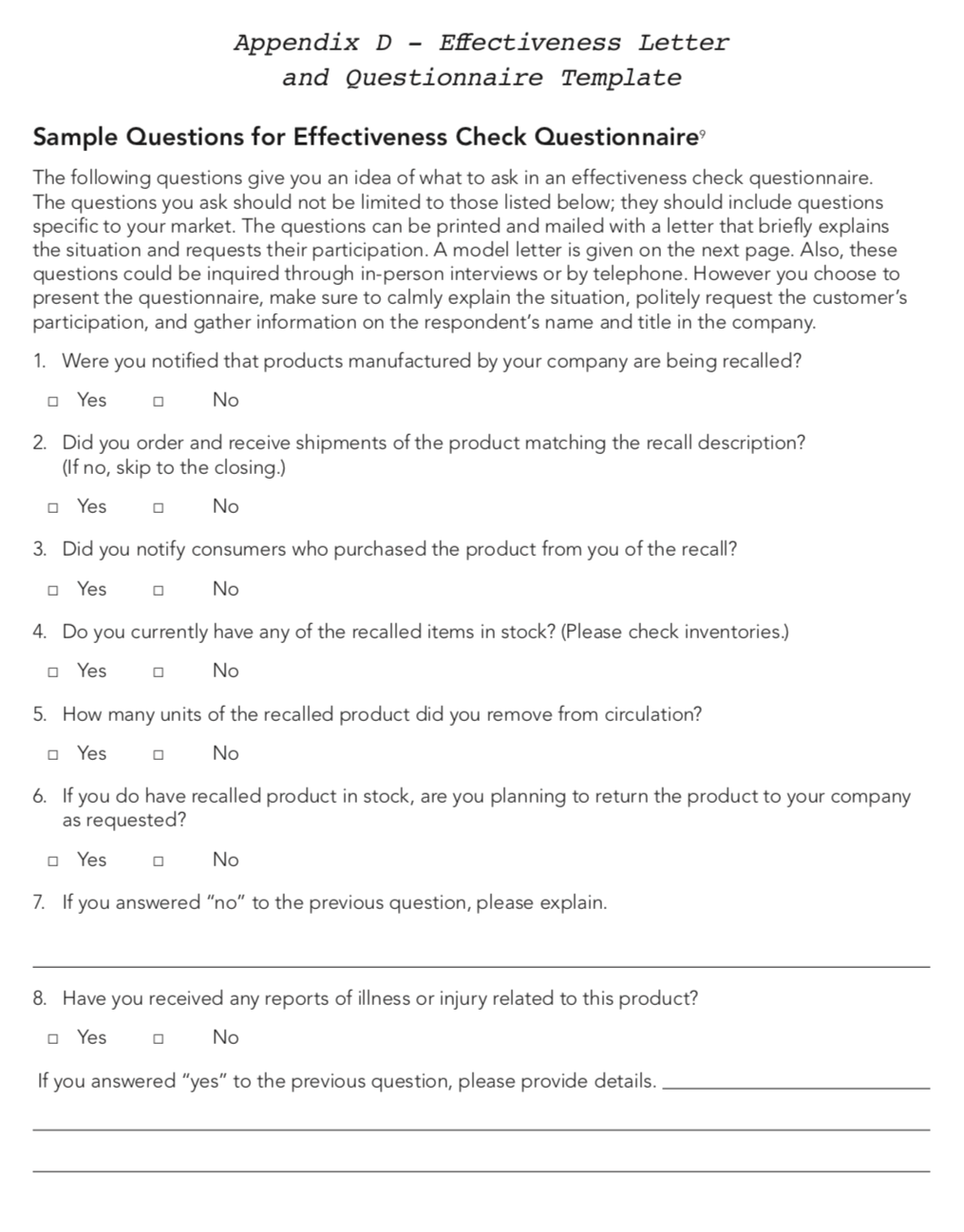
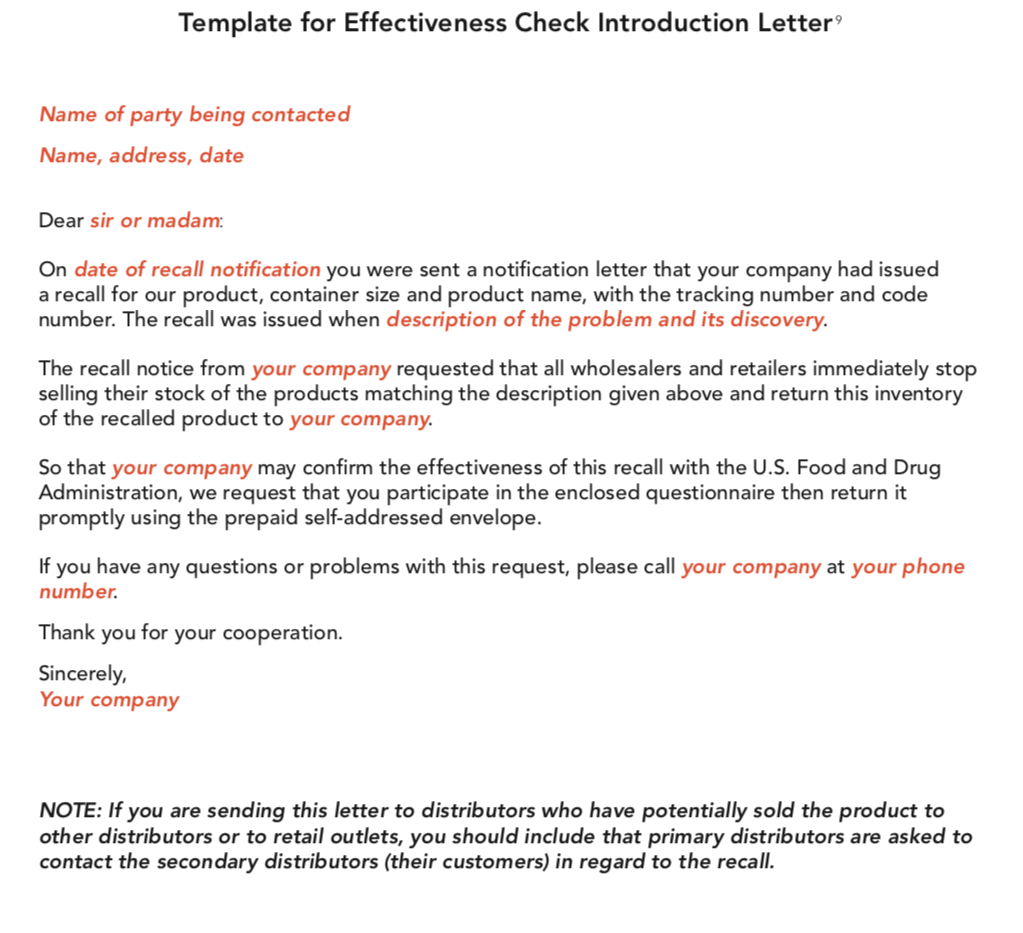
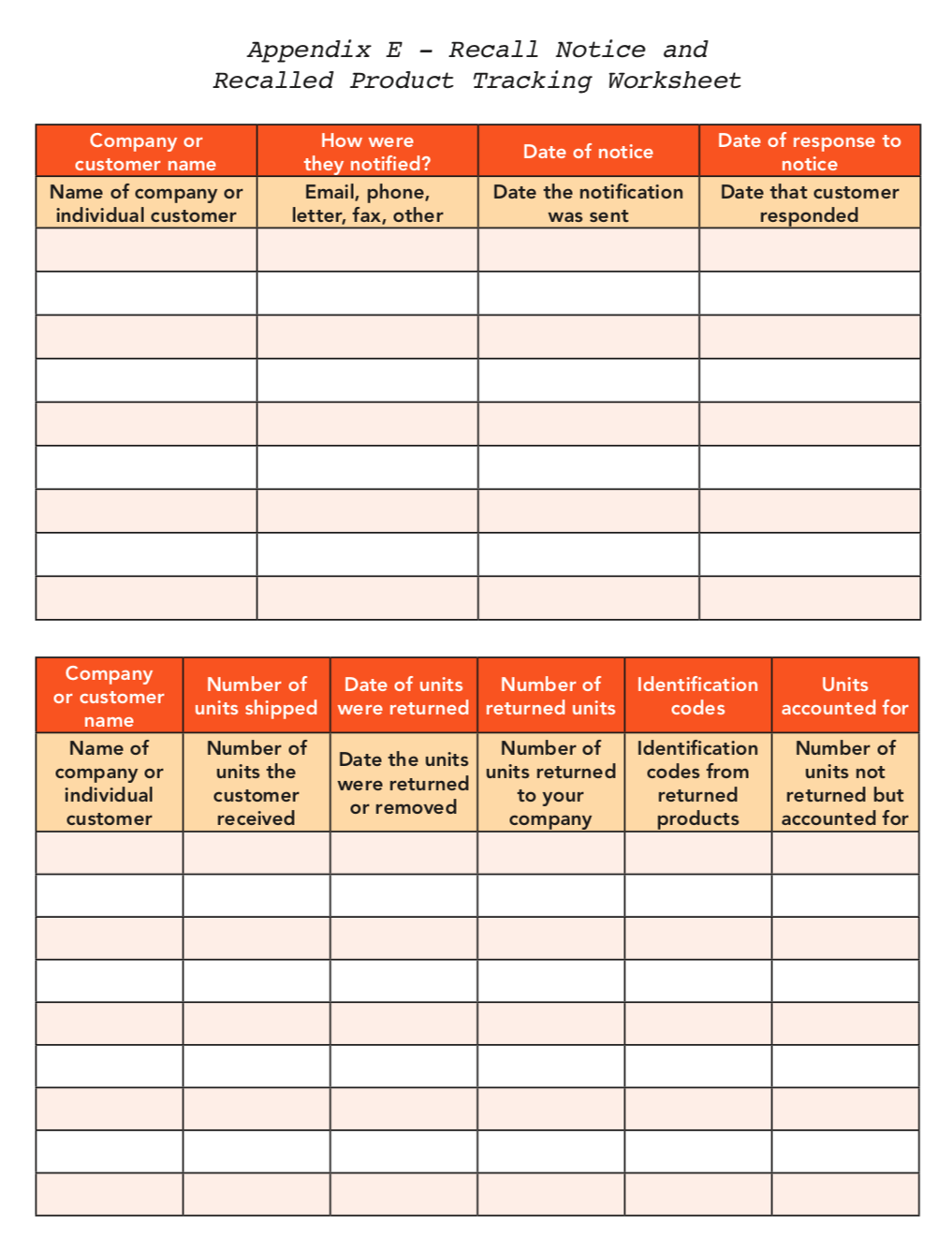
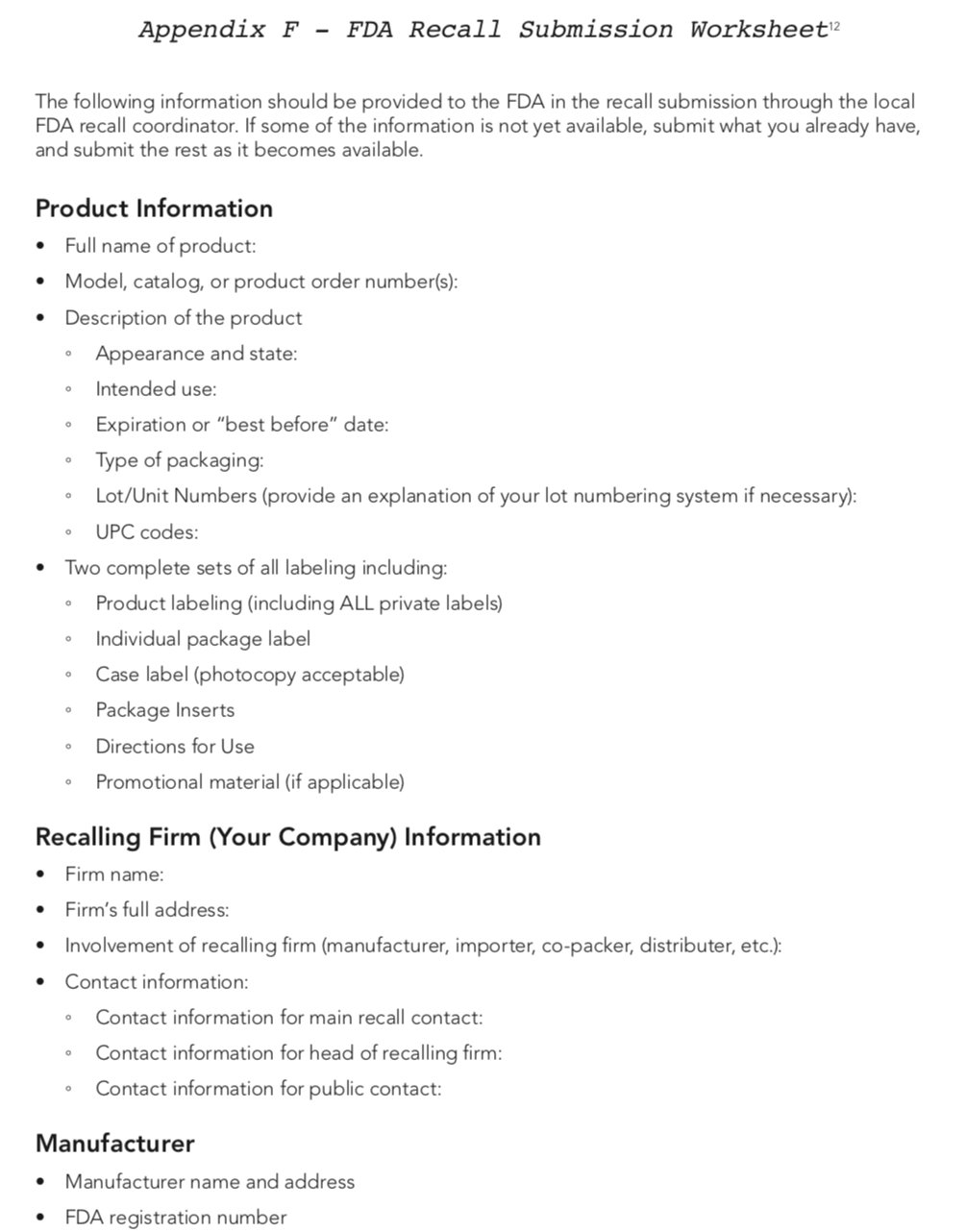
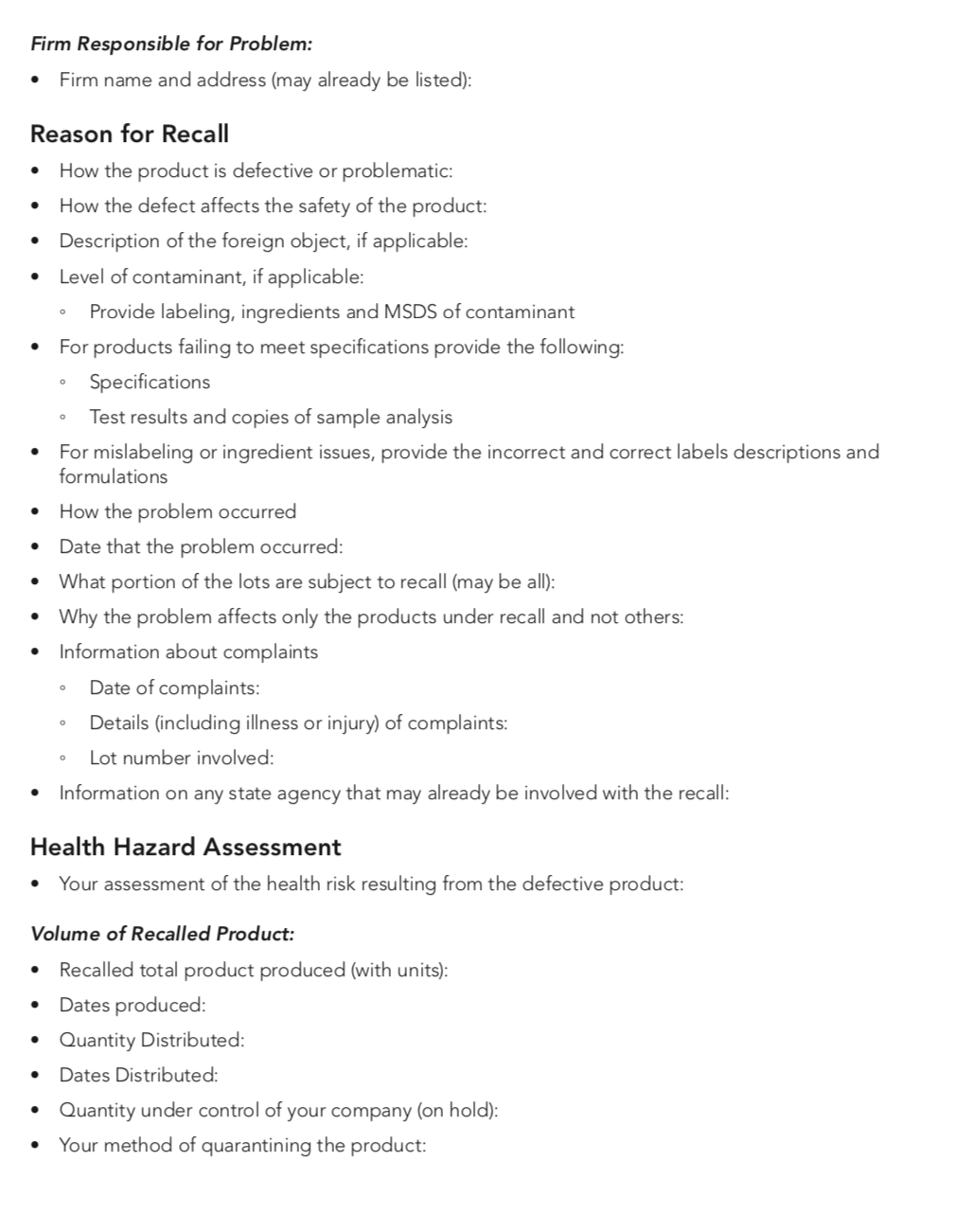
References:
1 U.S. Department of Agriculture. Food Safety and Inspection Services. (2013). FSIS Directive 8080.1 How to develop a meat and poultry product recall plan. Retrieved from http://www.fsis. usda.gov/wps/wcm/connect/d87d635d-75fa-4a9b-8301-378675435a68/RecallPlanBooklet_0513. pdf?MOD=AJPERES
2 Abbott, H. (1991). Managing product recall. Long Acre, London: Pitman Publishing.
3 Frush, K., Pleasants, J., Shulby, G., Hendrix, B., Berson, B., Gordon, C., & Cuffe, M. (2009). Blending technology and teamwork for successful management of product recalls. (12 ed., Vol. 84, pp. 1713- 1718). Association of American Medical Colleges.
4 Kramer, M., Coto, D., & David, W. (2005). The science of recalls. (1 ed., Vol. 71, pp. 158-163). Baltimore, MD: EHA Consulting Group.
5 U.S. Food and Drug Administration: Industry Guidance. Allergens Model Press Release.
6 U.S. Food and Drug Administration: Industry Guidance. Listeria Monocytogenes Model Press Release.
7 U.S. Food and Drug Administration: Industry Guidance. Clostridium botulinum Model Press Release.
8 U.S. Food and Drug Administration: Industry Guidance. Salmonella Model Press Release.
9 U.S. Food and Drug Administration: Industry Guidance. Information on Recalls of FDA Regulated Products.
10 U.S. Food and Drug Administration: Industry Guidance. E. coli Model Press Release.
11 California Department of Public Health. Sample Recall Plan. Retrieved from https://www.cdph. ca.gov/Programs/CEH/DFDCS/CDPH%20Document%20Library/FDB/FoodSafetyProgram/ FoodRecalls/SampleRecallPlan.pdf
12 U.S. Food and Drug Administration: Industry Guidance. Product Recalls, Including Removals and Corrections. Retrieved from https://www.fda.gov/safety/recalls/industryguidance/ucm129259.htm
Status and Revision History
Published on May 17, 2019